Concrete Problems
Concrete is one of the most widely used building materials in India. While it offers a lot of advantages, it is not without its issues. Individuals who are not aware of these problems or those who do not know how to fix them may face significant issues in the long run. In this article, we explore the 15 most common concrete problems faced by individuals and provide practical solutions to address these issues.
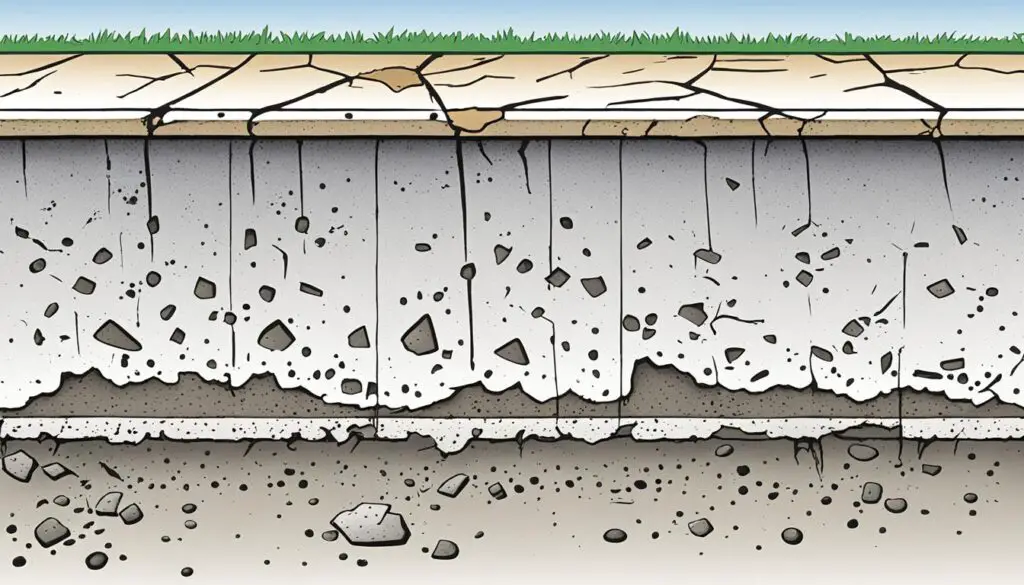
Key Takeaways:
- Concrete problems can decrease the longevity and functionality of concrete structures.
- There are 15 most common concrete problems, including cracks, scaling, blistering, etc.
- Proper understanding and identification of these problems is the first step in addressing them.
- Preventative measures and solutions can be applied to ensure the longevity of concrete structures.
- Regular maintenance is essential in preserving the functionality and appearance of concrete projects.
Understanding Concrete and Its Grades in India
Concrete is a vital building material used in the construction industry for centuries. It is a composite material made of different components like cement, aggregates, and water. The mixture of these materials forms a strong and durable substance that can be molded into different shapes and sizes. When dried and hardened, it becomes a solid foundation for buildings, bridges, roads, and more.
In India, different grades of concrete are used based on the application and required strength. The Indian Standard Code for Concrete Design (IS 456:2000) specifies the different grades of concrete and their properties. The table below shows the different grades of concrete and their compressive strengths:
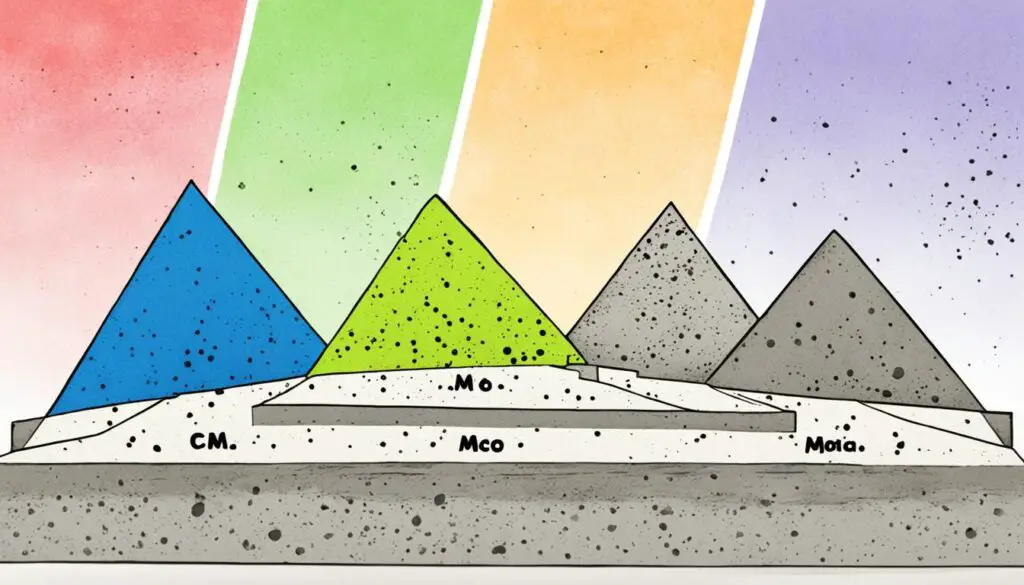
Table 1: Grades of Concrete Used in India
Grade | Concrete Mix Proportion (Cement:Sand: Aggregate) | Compressive Strength (MPa) |
---|---|---|
M5 | 1:5:10 | 5 |
M7.5 | 1:4:8 | 7.5 |
M10 | 1:3:6 | 10 |
M15 | 1:2:4 | 15 |
M20 | 1:1.5:3 | 20 |
M25 | 1:1:2 | 25 |
M30 | 1:0.75:1.5 | 30 |
M35 | 1:0.5:1 | 35 |
M40 | 1:0.25:0.5 | 40 |
Understanding the different grades and properties of concrete is crucial to determining the appropriate mix design based on the intended application. It ensures the concrete’s strength, durability, and longevity, which is vital in avoiding concrete problems like cracks and scaling.
Concrete Problems : Cracks in Concrete
Concrete structures are prone to cracking due to various factors. The most common types of cracks in concrete are:
Type of Crack | Cause |
---|---|
Plastic shrinkage cracks | Occurs when the concrete dries too quickly, causing cracks in the surface layer. |
Drying shrinkage cracks | Occurs when concrete dries out and shrinks, causing cracks. |
Settlement cracks | Occurs when the underlying soil settles, unevenly putting pressure on the concrete, leading to cracking. |
Structural cracks | Occurs due to poor reinforcement design, inadequate curing, or loading beyond the capacity of the concrete. |
Preventing cracks in concrete requires careful consideration during the mixing, pouring, and curing process, such as proper mix design, minimizing water content, and using proper curing techniques. Following these precautions can help mitigate the risk of cracks forming in your concrete structure.
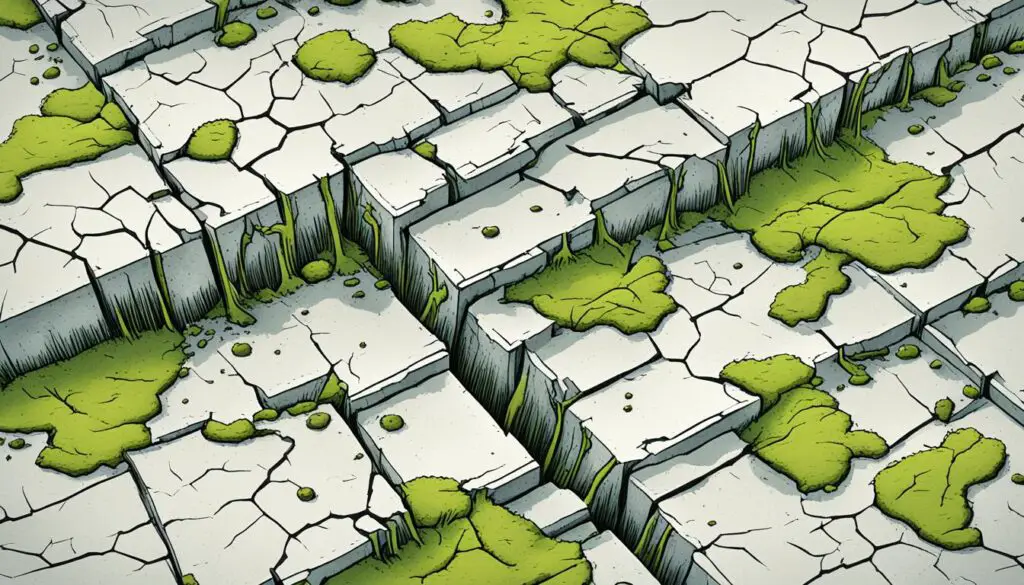
Concrete Problems: Bleeding in Concrete
Bleeding is a common problem experienced while working with concrete. Before addressing the issue, one must know the reasons behind its occurrence. Water moves to the surface by gravitational force due to the difference in specific gravities of cement and water. The reasons for bleeding include:
- Excessive water in the mix
- Poor grading of sand leads to a lack of finer particles
- Concrete with high workability and low viscosity
It is crucial to reduce bleeding as it compromises the structural integrity and strength of the concrete. Here are four ways to reduce bleeding:
Methods | Description |
---|---|
Reducing water | The amount of water in the mix should be reduced, as lower water content minimizes bleeding. |
Using admixtures | Admixtures such as air-entraining agents or supplementary cementitious materials can reduce bleeding. |
Adding fine aggregate and cement | An increase in fine aggregate and cement content in concrete reduces bleeding by increasing the viscosity of the mix. |
Concrete placement techniques | Proper concrete placement with appropriate vibration techniques can minimize bleeding while ensuring proper consolidation. |
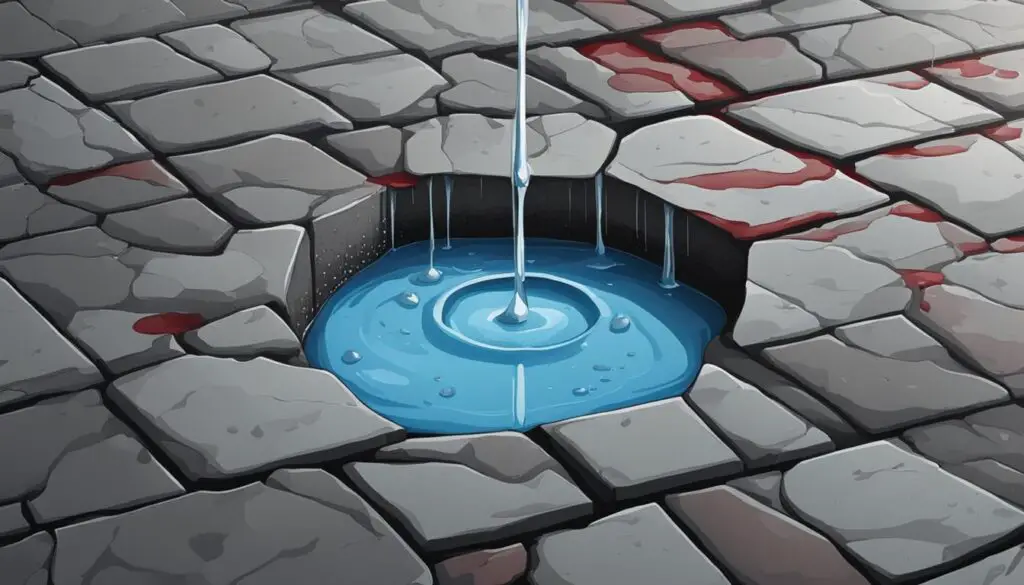
Concrete Problems: Segregation in Concrete
One of the common problems with concrete is segregation, which occurs when the components of the concrete mixture separate, resulting in an uneven mixture. This can affect the strength and durability of the concrete in the long run. To prevent segregation, the following six measures can be taken:
- Quality of materials: Ensure the use of good-quality materials, free from impurities, to maintain the uniformity of the mixture.
- Mixing: The mixing should be done correctly and thoroughly to ensure that all the components are uniformly distributed.
- Timing: The concrete should be transported and placed within the recommended time limit to avoid the risk of segregation.
- Transportation: The concrete should be transported in a manner that does not cause segregation.
- Vibration: Adequate vibration should be applied to the concrete to ensure proper compaction and eliminate any voids that may cause segregation.
- Water-to-cement ratio: The water-to-cement ratio should be appropriate to ensure the right consistency of the mixture and prevent segregation.
By following these steps, the uniformity and durability of the concrete can be maintained, preventing segregation and ensuring the longevity of the structure.
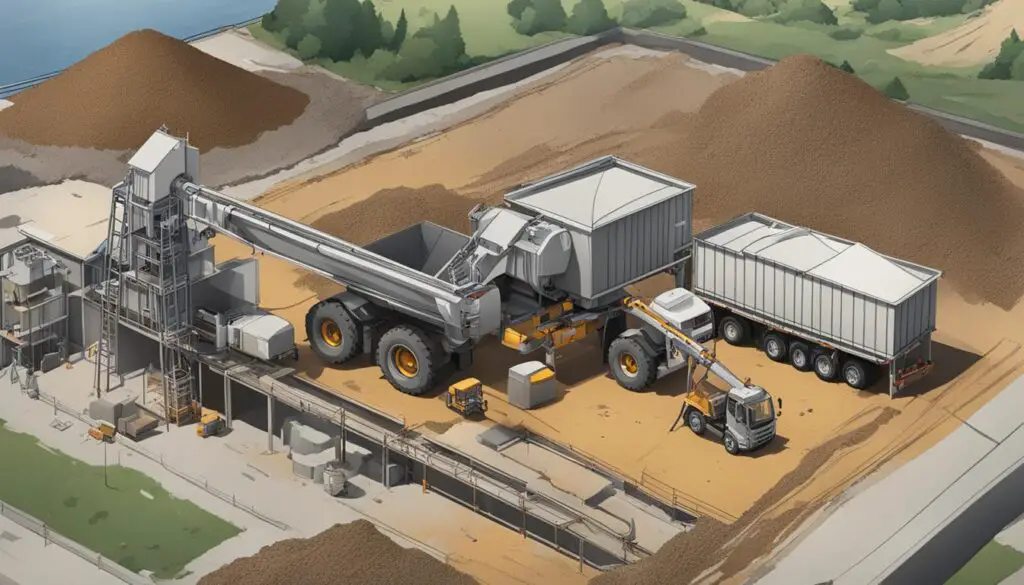
Concrete Problems: Scaling in Concrete
Scaling is a common problem that occurs when the concrete surface flakes or peels due to freeze-thaw cycles or improper curing. Not only does this diminish the aesthetic appeal of the concrete, but it also compromises the structural integrity of the concrete over time.
To prevent scaling, individuals should implement the following five effective methods:
- Avoid overworking the surface: Overworking the surface during finishing can cause the water to rise and collect on the surface, leading to scaling.
- Proper implementation of air-entrained concrete: Air-entrained concrete is more resistant to freeze-thaw cycles and thus can prevent scaling.
- Prevent exposure to moisture before curing: Moisture exposure before the concrete has adequately cured can lead to scaling.
- Use of proper curing methods: Proper curing methods such as sealing, membrane-forming curing compounds, and curing blankets can prevent scaling.
- Implementation of proper maintenance practices: Regular inspection and maintenance can prevent scaling by addressing potential issues before they worsen.
By following these solutions, individuals can prevent scaling in concrete and ensure the longevity and functionality of their concrete structures.
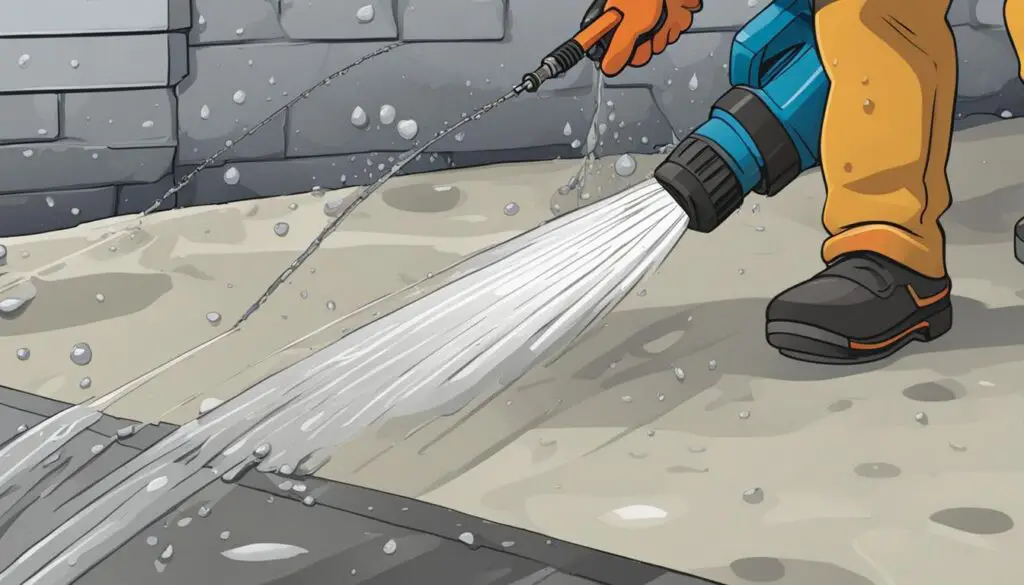
Concrete Problems: Laitance in Concrete
In the construction industry, laitance is a common term used for the fine particles that accumulate on the surface of hardened concrete. Laitance formation is a natural outcome of the water and cement mixture’s reaction and the resulting sediment that rises to the surface. However, an excess of laitance can lead to a rough, porous surface that is both unsightly and undesirable.
If left ignored, the accumulation of laitance can impact the durability of the concrete, making it more susceptible to damage due to weather, abrasion, and chemical exposure. To prevent laitance buildup, it is necessary to be mindful of the mix’s water-cement ratio, surface finishing techniques like troweling, and proper curing methods.
Preventing laitance formation can ensure a smooth, level, and durable concrete finish that enhances both the visual and functional aspects of any structure.
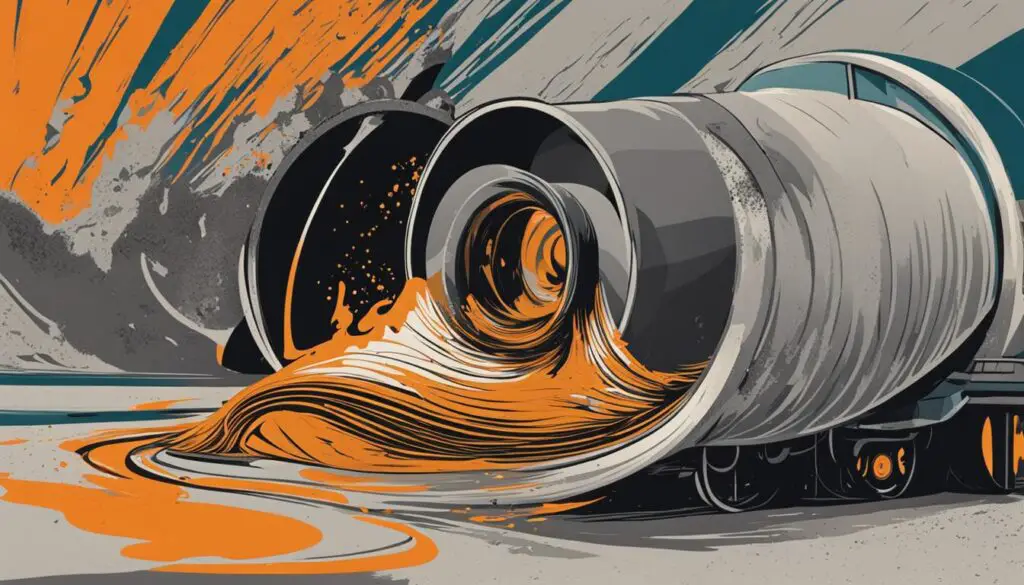
Methods to Prevent Laitance Formation:
Method | Advantages |
---|---|
Proper concrete mix design | Specific water-cement ratio reduces excess water and helps avoid laitance buildup |
Use of anti-laitance admixtures | Reduces the water content, ensuring a stronger final product that is more resistant to weathering and chemical exposure. |
Finishing Techniques | The use of power trowels for surface finishing ensures a smooth and level final surface that is resistant to laitance buildup |
Curing Methods | Proper curing methods like coverings to protect the concrete from direct sunlight and other weather conditions can help prevent laitance buildup |
Resurfacing | If laitance buildup is severe, resurfacing the concrete can eliminate the problem by stripping the rough surface and creating a smooth and level surface |
By taking proper precautions and implementing the methods mentioned above, individuals can prevent laitance buildup in their concrete structures effectively, ensuring a long-lasting and functional final product.
Concrete Problems: Dusting in Concrete
Dusting is a common issue faced by many individuals who work with concrete. It refers to the formation of a powdery layer on the concrete surface, which can be caused by over-troweling or a high water-to-cement ratio. In addition to affecting the appearance of the concrete, dusting can also compromise its structural integrity. However, there are several ways to stop concrete dusting in its tracks:
- Use a good quality concrete sealer: Applying a sealer can help to prevent the formation of dust on the concrete surface.
- Reduce water in the mix: Using less water in the concrete mix can help to prevent dusting caused by a high water-to-cement ratio.
- Use a curing compound: Applying a curing compound to the concrete’s surface can prevent the formation of dust and enhance its overall durability.
- Add a hardening agent: Adding a hardening agent to the concrete mix can greatly reduce the likelihood of dusting.
By implementing these preventative measures, individuals can stop concrete dusting and maintain the strength and appearance of their concrete structures.
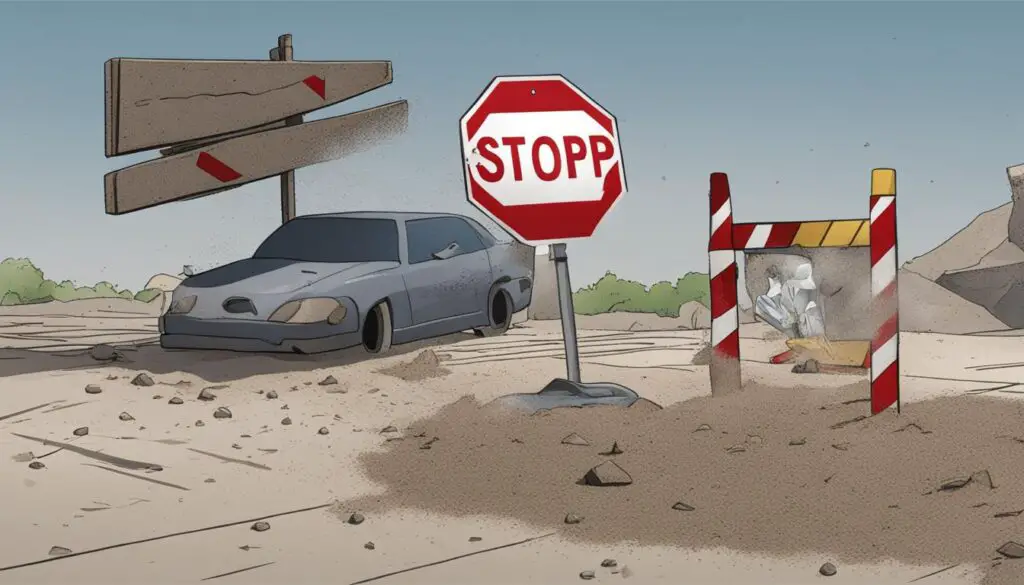
Concrete Problems: Spalling in Concrete
Spalling can be a frustrating problem for individuals dealing with concrete structures. It occurs when the surface of the concrete chips or breaks off, revealing the underlying layers. This can lead to structural instability and significantly reduce the longevity of the concrete.
To stop concrete spalling, it is vital to identify the root cause of the problem, which could be due to various factors such as moisture, corrosion of reinforcing steel, and freeze-thaw cycles.
One effective method for preventing spalling is to ensure adequate concrete cover for the reinforcing steel. This can be achieved by using epoxy coatings, sealants, and other protective coatings to ensure the steel is not exposed to harmful elements.
Another effective measure to stop concrete spalling is by using air-entrained concrete. The microscopic air bubbles in the concrete allow moisture to expand and contract without damaging the concrete surface or reinforcing steel.
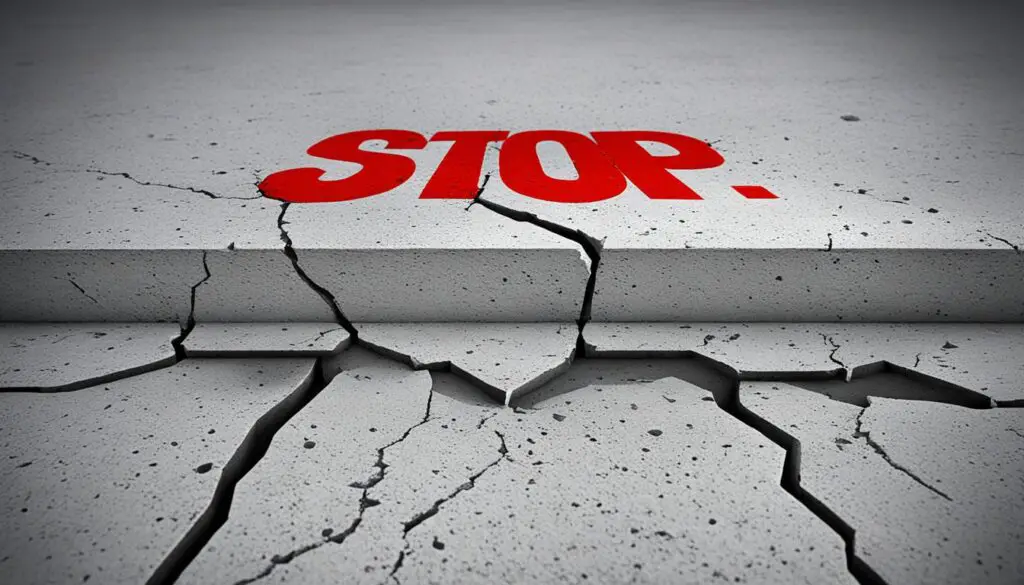
Lastly, avoid using de-icing chemicals and use protective coatings to stop moisture from penetrating the concrete surface. These measures will ensure that your concrete structures remain strong, durable, and aesthetically pleasing for many years.
Concrete Problems: Discoloration in Concrete
Discoloration refers to changes in color that can occur on the concrete surface due to various factors. These factors include the use of improper materials, inadequate curing, and exposure to harsh weather conditions. Preventing concrete discoloration is essential in maintaining the desired appearance of the concrete.
Preventing Concrete Discoloration
There are practical ways to prevent concrete discoloration. One of the most effective ways is to use high-quality concrete materials that are suitable for the specific project. Ensure the materials comply with the standards set by the local regulatory bodies.
Another way to prevent discoloration is to ensure proper curing. Concrete should be wet-cured for at least seven days to reduce the risk of discoloration. During the curing process, keep the concrete surface moist to prevent cracking and discoloration.
Finally, protect the concrete from exposure to harsh weather conditions by applying a suitable sealant or protective coating. This will minimize staining from oil, chemicals, and other substances that may discolor the concrete surface.
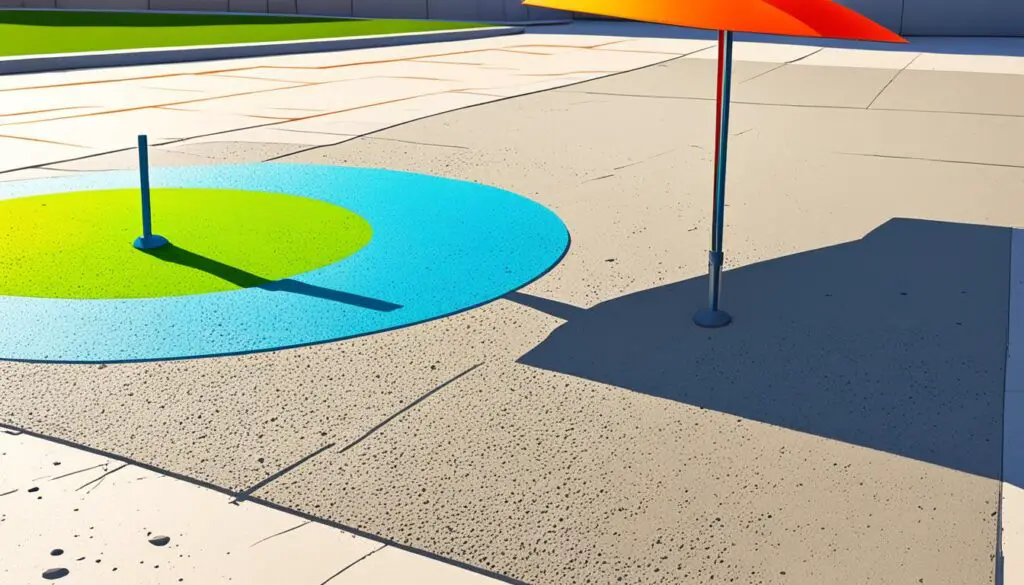
“Preventing discoloration in concrete not only ensures the desired appearance of the project but also maintains the structural integrity of the concrete.”
Concrete Problems: Crazing in Concrete
Crazing refers to the formation of fine cracks on the surface of concrete structures. While it does not affect the structural integrity of the concrete, it can lead to a deterioration in its aesthetics over time, causing concern for many homeowners and businesses. Crazing is caused by shrinkage of the concrete surface, which occurs during the curing process.
To stop concrete crazing, it’s important to use a high-quality concrete mix that is formulated for shrinkage control. Additionally, proper curing techniques such as extending the moist curing duration and keeping the concrete surface wet can help prevent crazing. Another effective way to stop concrete crazing is by applying a curing compound or sealant that will help slow down the drying process.
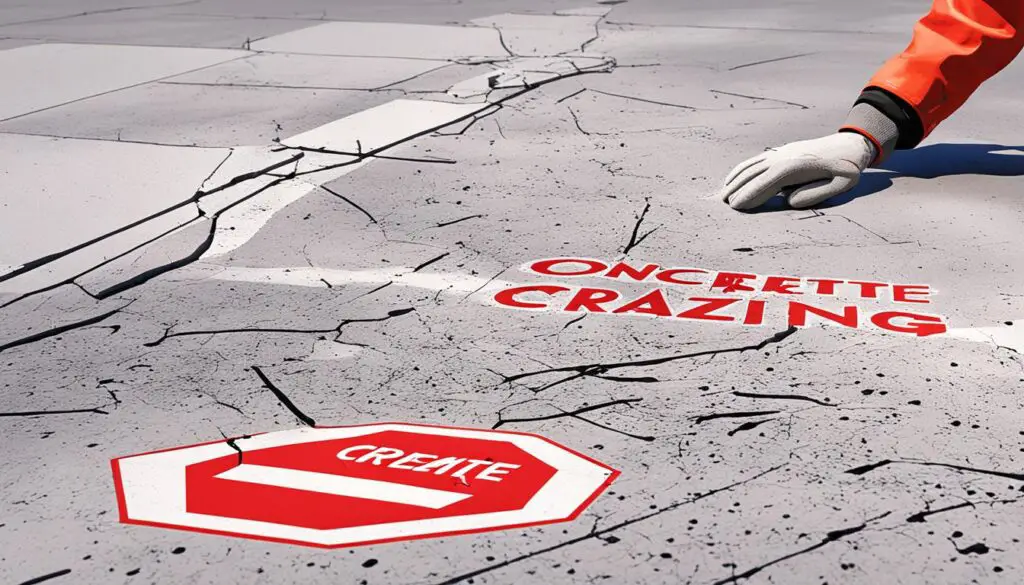
Regular inspection and maintenance can help detect cracks early on and prevent further damage. It is important to consult with a professional to assess any cracks and determine the best course of action to stop concrete crazing.
Concrete Problems: Efflorescence in Concrete
Efflorescence is a common problem that affects the appearance and longevity of concrete structures. When white or grayish crystals appear on the concrete surface due to salt deposits, it can be frustrating for architects and contractors. Fortunately, there are methods to prevent this issue from occurring, ensuring a clean and attractive concrete finish.
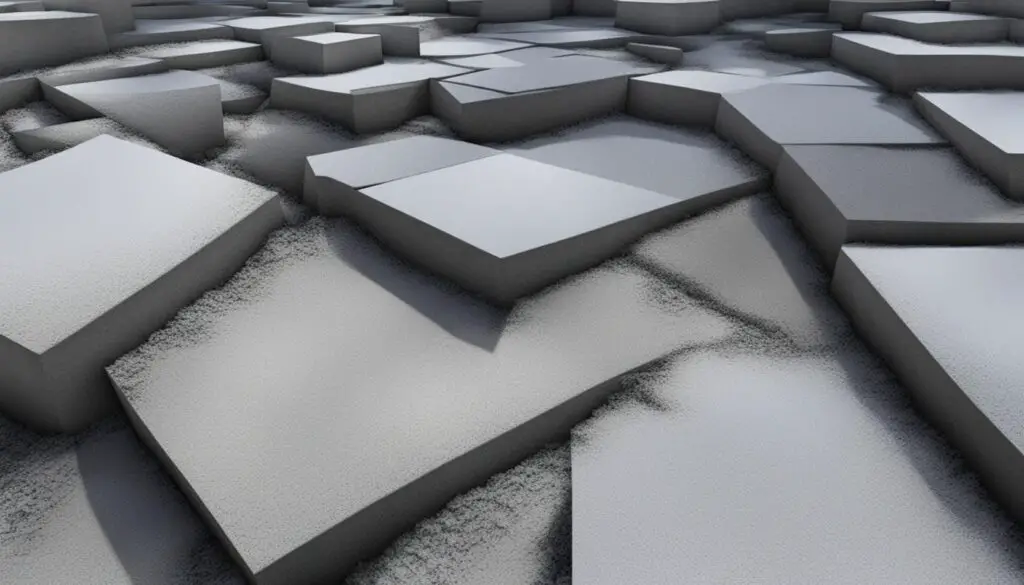
One way to prevent efflorescence is to use high-quality concrete that is less prone to salt deposits. Additionally, proper drainage and ventilation can reduce moisture buildup, which is a common cause of efflorescence.
Another effective method to prevent efflorescence is to use a concrete sealer that blocks moisture and salt penetration. Sealers can be applied during or after construction and provide a protective barrier against water, chemicals, and other damaging substances.
Overall, preventing efflorescence requires attention to detail and proper planning. By following these preventative measures, individuals can ensure a long-lasting, aesthetically pleasing concrete structure that is free from efflorescence.
Concrete Problems: Curling in Concrete
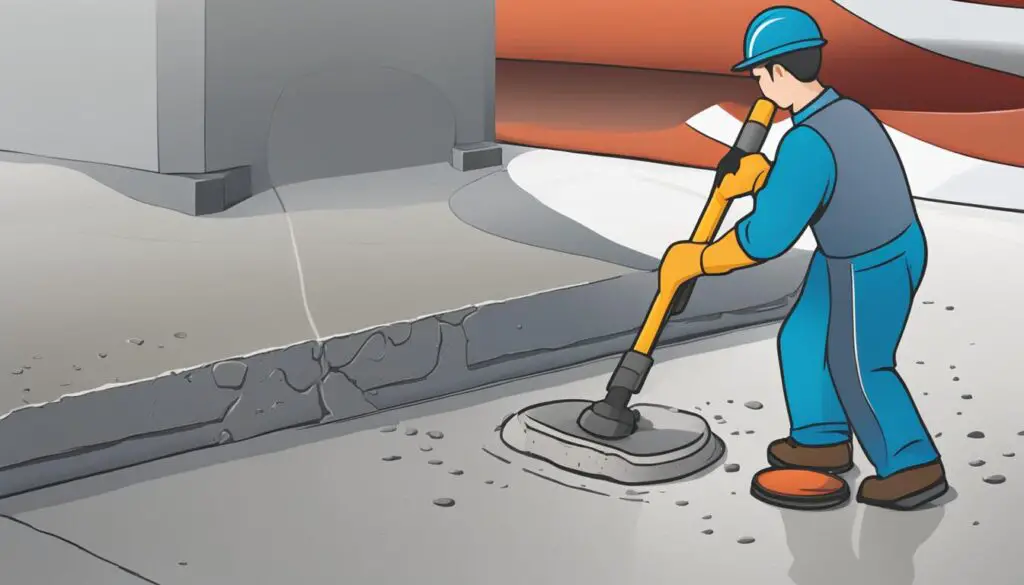
Curling in concrete is a common problem faced in construction. It occurs when the edges of concrete slabs curl upwards, leading to various issues such as poor flatness, cracking, and safety concerns. To prevent concrete curling, here are some practical methods you can implement:
- Ensure that the subgrade has adequate compaction to prevent differential settlement.
- Use low-slump concrete with a high coarse aggregate content to provide sufficient internal support.
- Install properly designed and spaced joints to relieve stress.
- Maintain proper curing conditions to prevent moisture loss.
- Use high-quality finishing techniques to properly level the concrete surface.
By following these preventative measures, you can ensure a flat and level concrete surface that is both safe and durable.
Concrete Problems: Blistering in Concrete
Blistering is a common problem encountered in concrete, characterized by the formation of small bumps or blisters on the concrete surface. This can be caused by various factors, including the presence of excess moisture, high temperatures, and the use of incompatible materials.
Prevention is key when it comes to blistering in concrete. To prevent the formation of blisters, ensure that concrete is not overworked during placement and finishing, as this can lead to the trapping of excess moisture. Additionally, avoid placing concrete in high temperatures, as this can cause rapid drying and blistering. Using high-quality materials that are compatible with each other is another crucial step in preventing concrete blistering.
Practical Ways to Prevent Blistering in Concrete:
- Avoid overworking concrete during placement and finishing
- Avoid placing concrete in high temperatures
- Use high-quality materials that are compatible with each other
- Ensure that the concrete mix has the correct proportion of water, sand, and cement
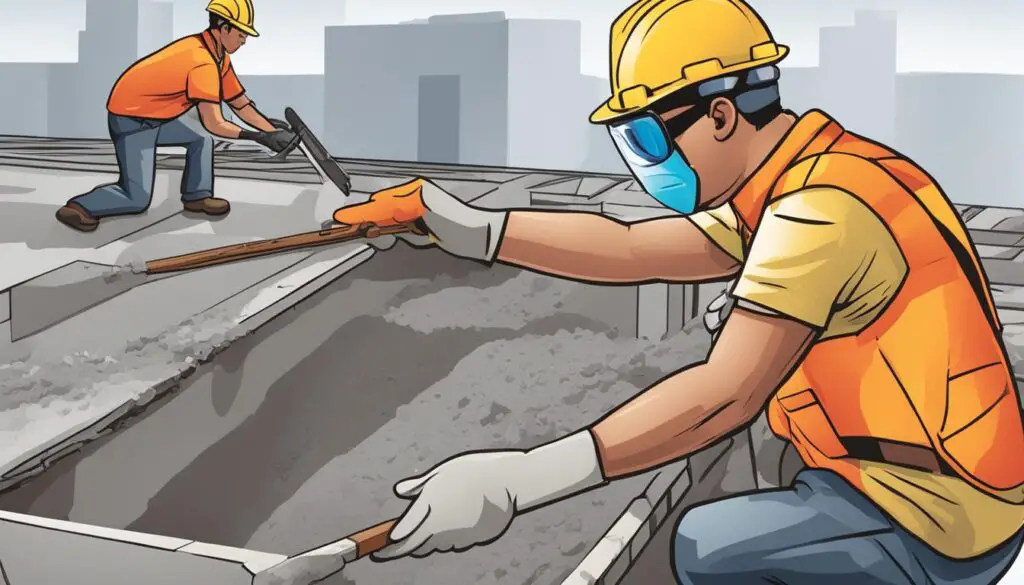
Expert Tip: If blistering has already occurred, the affected area should be allowed to dry before removing the blistered material. A concrete patching material can then be used to fill the area and restore the surface of the concrete.
Conclusion
Concrete is a popular building material in India due to its durability and strength. However, it is not immune to problems such as cracks, bleeding, scaling, and efflorescence. By understanding the common concrete problems and their solutions discussed in this article, individuals can take proactive steps to prevent these issues from occurring or worsening.
Preventative measures such as proper curing, correct mixing of components, and timely repairs can ensure the longevity and sustainability of concrete structures. It is essential to use the appropriate grade of concrete for each construction project and understand its composition and quality.
By following the practical solutions and precautions discussed in this article, individuals can avoid costly repairs and maintain the aesthetic appeal and functionality of their concrete structures. Stay informed and take action to keep your concrete projects in excellent condition for years to come.
Thanks For the Great Attention!
Good Bye & Take Care
Happy Learning
Also, Read,