Quality control of concrete is crucial in ensuring that construction projects meet the highest standards of quality, durability, and compliance with regulations. The process involves several factors that are essential to achieving effective quality control of concrete. In this article, we will discuss the five key advantages of quality control of concrete, as well as the seven important factors that impact its effectiveness.
Key Takeaways
- Quality control of concrete is essential to ensure the success and durability of construction projects.
- There are five main advantages of quality control of concrete, including enhanced structural integrity, improved durability, consistent performance, cost savings, and compliance with standards and regulations.
- The effectiveness of quality control of concrete depends on seven important factors, including proper materials selection, accurate proportions and mixing, and proper curing techniques.
- Construction professionals must prioritize quality control of concrete to meet industry standards and regulations and ensure the long-term performance of structures.
- Incorporating quality control measures can result in significant cost savings in the long run by avoiding potential failures and repairs.
Importance of Quality Control in Construction Projects
Quality control is integral to construction projects, and concrete is no exception. It serves as the backbone of any structure and demands appropriate attention. Quality control ensures that the concrete used in construction complies with industry standards and meets regulatory requirements to ensure safety, longevity, and durability. Neglecting quality control can lead to significant structural damage, expenses related to repairs, and a potential threat to human lives.
Quality control in construction projects encompasses multiple measures to ensure the highest level of safety and quality. From proper materials selection to accurate proportions, the success of the project depends on each critical stage of quality control in concrete. Attention to detail is fundamental in every step of the process to ensure quality assurance and quality control are in place.
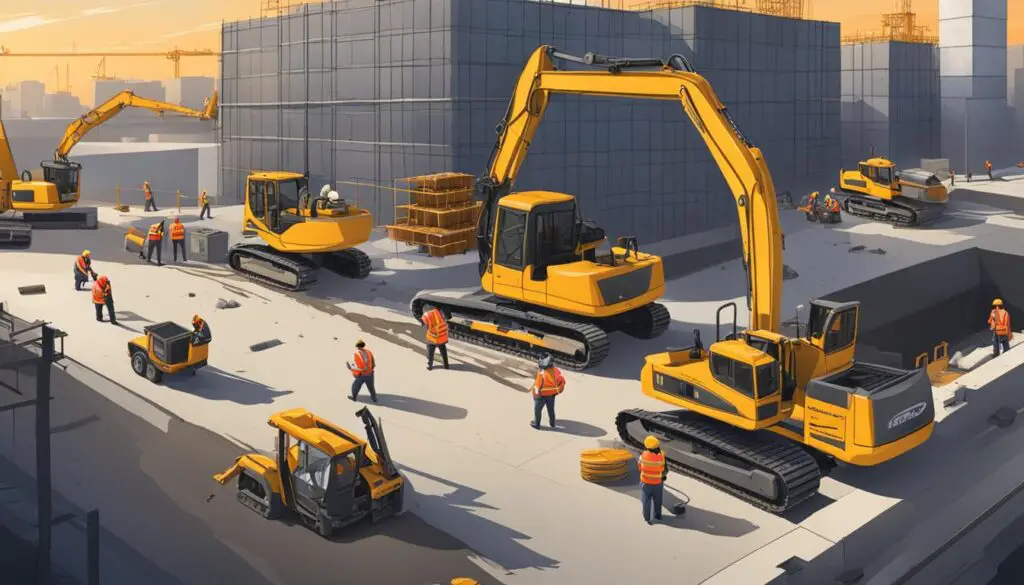
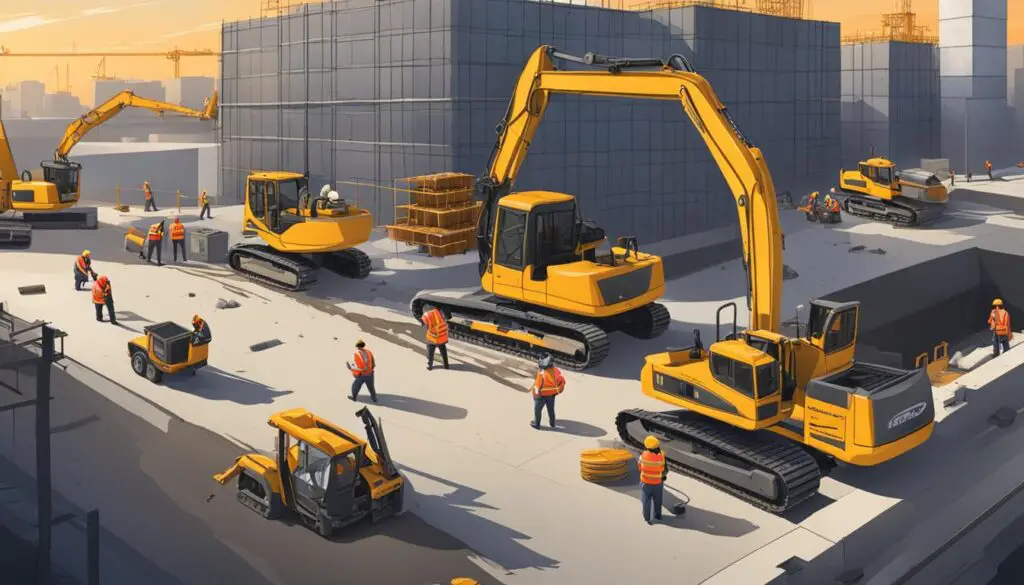
The significance of quality control in construction projects
Quality control prevents structural failures, saves time and money, and increases the overall sustainability of structures. It guarantees that the final products meet regulatory, project, and client standards. Beyond the economic implications, quality control measures ensure that engineers, workers, and the public at large remain safe. Incorporating quality control into construction ensures optimal results for the investor and stakeholders alike.
“Quality is never an accident. It is always the result of intelligent effort.”
How quality control impacts the durability of structures
When constructors adhere to proper quality control measures, the result is an increase in the long-term performance and sustainability of the final product. Concrete structures that undergo quality control measures are less liable to damage and maintain their functionality for extended durations of time. It is important to note that material strength is the foundation of structural durability.
Compliance with regulations
Construction regulatory bodies enforce quality control regulations to ensure smooth construction processes and structural durability. Adhering to such regulations, including choosing materials that abide by the laid-out standards, results in successful projects that are compliant with regulations. Making use of subpar materials is a recipe for disaster in any construction project, given that subpar materials lead to inferior outcomes.
Enhanced Structural Integrity
Effective quality control of concrete provides several benefits to construction projects. One of the key advantages is the enhanced structural integrity of the final product. By adhering to strict quality control measures, the risk of cracks, deterioration, and other structural issues is significantly reduced, resulting in a more robust and durable structure.
Proper quality control measures ensure that the concrete mix complies with industry standards and regulations. This helps to avoid any weak points in the structure that could be vulnerable to environmental factors, such as freeze-thaw cycles or seismic activity. Additionally, quality control measures help to detect any inconsistencies in the concrete mix before it is poured, allowing for adjustments to be made to improve the final product.
Enhanced structural integrity is particularly important in large-scale construction projects, such as high-rise buildings or bridges, where safety and longevity are critical factors. By ensuring high-quality concrete, construction professionals can feel confident that their structures will perform as expected, even under extreme conditions.
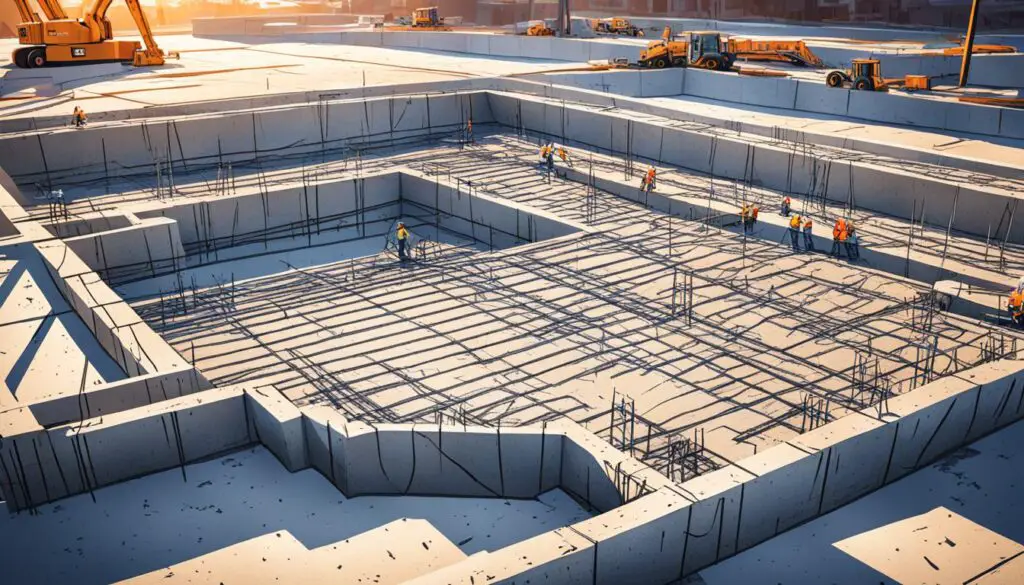
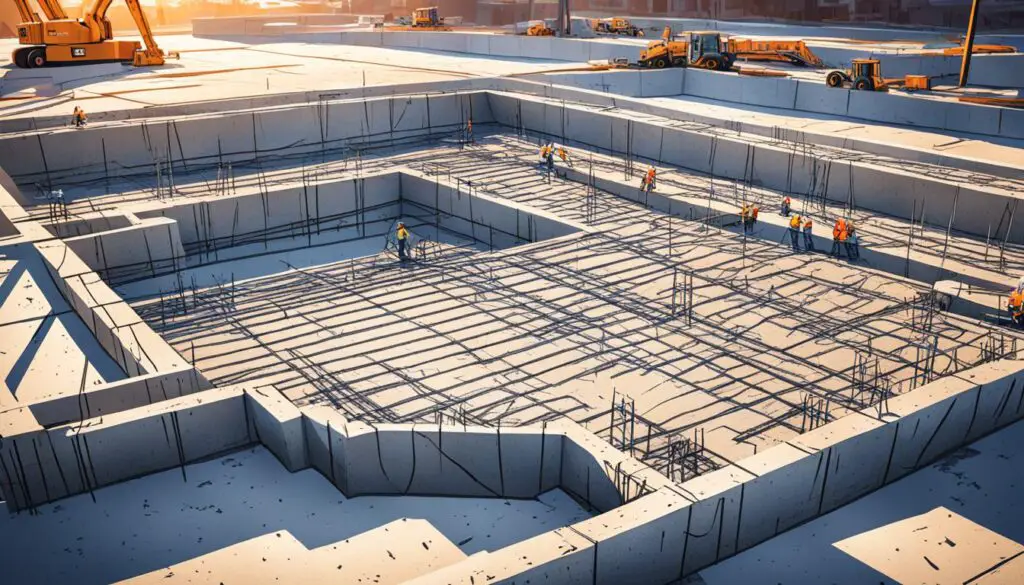
Improved Durability and Longevity
Quality control of concrete is essential for constructing long-lasting and durable structures. By adopting strict quality control measures, the concrete used in construction projects can achieve the desired level of durability and sustainability. Through proper mixing, curing, and testing, quality control ensures that the concrete can withstand harsh weather conditions, heavy loads, and other challenges that could damage inferior concrete.
Proper quality control measures also contribute to improving the longevity of concrete structures. With a longer lifespan, structures built with quality-controlled concrete require fewer repairs and replacements, saving construction professionals time and money in the long run.
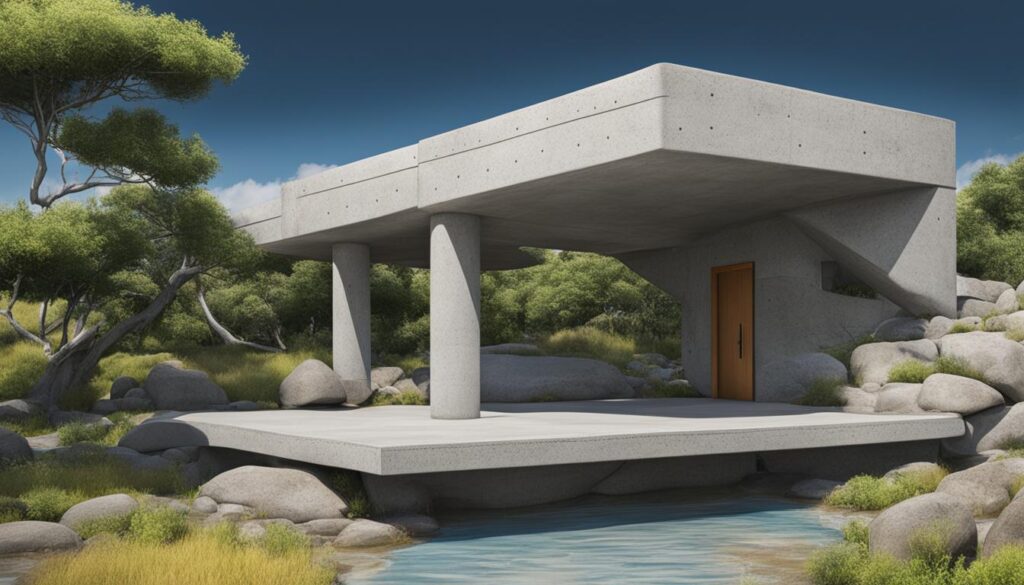
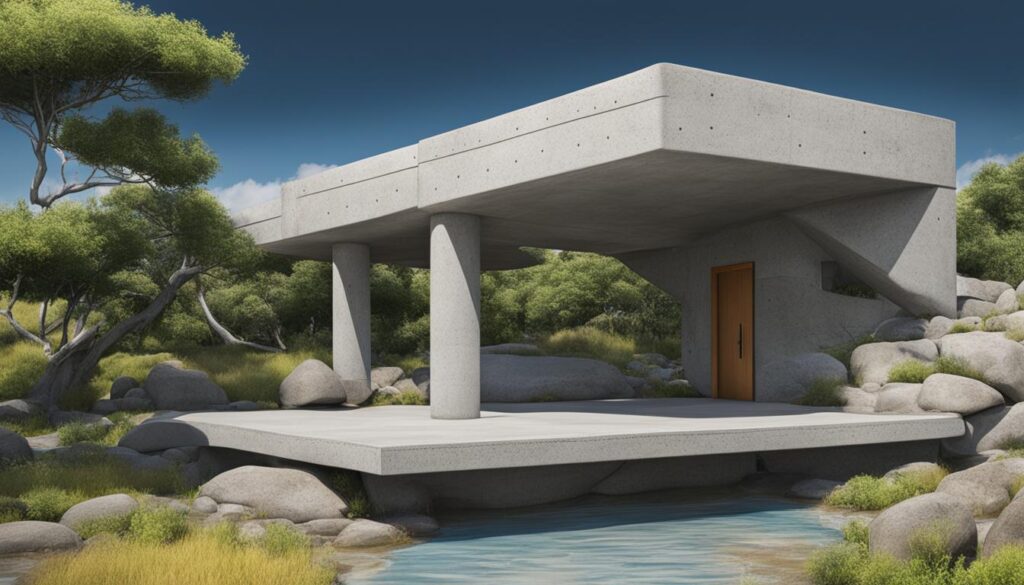
Quality control of concrete leads to improved durability and increased longevity of structures.
Consistent Performance
Ensuring consistent performance is crucial in any construction project, and quality control of concrete plays a vital role in achieving this. By adhering to industry standards for quality control, construction projects can produce consistent and high-quality concrete that performs to the same high standard across all areas of the structure, regardless of location or intended use.
By eliminating any inconsistencies in the production and use of concrete, quality control benefits the overall durability, performance, and safety of the structures built using it. With consistent performance, there is less likelihood of cracks or other structural issues developing over time.
Consistent Performance Benefit | Description |
---|---|
Uniform Strength | Concrete produced by proper quality control measures has uniform strength, which means that each section of the structure will have the same strength and, therefore, equal weight-bearing capacity. |
Reduced Shrinkage | With consistent concrete performance, there is less likelihood of shrinkage occurring, leading to fewer cracks and structural issues. |
Increase in Structural Integrity | By achieving consistent performance throughout the structure, the overall structural integrity is improved, leading to better durability and longevity. |
Implementing quality control of concrete ensures that contractors can deliver high-quality structures on time and within budget, meeting the expectations of their clients and other stakeholders. It provides a reliable and consistent approach that helps to minimize the risk of any unforeseen problems or faults.
Cost Savings
One of the major benefits of implementing quality control measures in concrete construction projects is the significant cost savings it can provide in the long run. By using high-quality concrete that has undergone proper quality control, project managers can avoid potential issues and failures that can result in costly repairs and replacements.
Investing in quality control during the construction phase may require upfront costs, but in the long run, it can lead to substantial savings. Proper quality control measures result in a more durable and long-lasting concrete product, reducing the need for future repairs and replacements. This will save construction companies both time and money, as the need for ongoing maintenance and upkeep is significantly diminished.
Compliance with Standards and Regulations
Meeting industry standards and regulations is critical in ensuring that construction projects are safe, durable, and meet the required legal requirements. Compliance with standards and regulations is one of the essential benefits of quality control of concrete.
A comprehensive quality control program ensures that the concrete used in construction adheres to all relevant standards and regulatory requirements. Compliance with these standards and regulations is necessary to ensure that the constructed buildings are safe, structurally sound, and meet the required quality standards.
Regulations and standards for construction projects vary depending on the location and type of project. However, quality control ensures that the concrete products used in construction meet the minimum requirements for strength, durability, and safety.
Examples of Standards and Regulations for Concrete Products
Regulation | Description |
---|---|
American Concrete Institute (ACI) | ACI sets the standards and guidelines for the manufacture and use of concrete products in construction. |
ASTM International | ASTM standards are used worldwide to specify and test materials used in construction, including concrete products. |
National Ready Mixed Concrete Association (NRMCA) | NRMCA works to advance the use of ready-mixed concrete by providing education, technical support, and advocacy. |
Compliance with regulations and standards is necessary to ensure that quality concrete products are produced and used in construction projects. Quality control of concrete is an essential factor in maintaining regulatory compliance and ensuring that the final product meets all necessary quality standards.
Factors Affecting the Quality Control of Concrete
Quality control in concrete is an essential process that ensures the final product meets the desired quality standards. Several factors influence the effectiveness of quality control in concrete, including:
Factors | Description |
---|---|
Adherence to Specifications | Strict adherence to specifications and standards is crucial to achieving effective quality control of concrete. This ensures that the final product meets expected quality outcomes and performs adequately over time. |
Proper Materials Selection | The selection of appropriate materials is fundamental in the quality control of concrete as these affect the overall durability, strength, and performance of the final product. |
Accurate Proportions and Mixing | Ensuring the correct proportions and consistent mixing techniques significantly contribute to effective quality control throughout the concrete mixing process. |
Curing and Drying Process | Proper curing and drying techniques are essential in achieving desired quality outcomes in the final product during the concrete setting process. |
Environmental Factors | The environmental conditions during concrete placement, consolidation, and finishing can impact the product’s quality outcomes and performance. |
Transportation and Handling | The handling and transportation of concrete from the mixing to the placement site can affect the product’s quality performance if not carefully monitored. |
Testing and Inspection | Proper testing and inspection techniques provide an objective measure of the quality control of concrete. This ensures compliance with industry standards and requirements and prevents potential structural failure. |
Understanding these essential factors can significantly improve the quality control of concrete, ensuring long-term performance and sustainability in construction projects.
Factor 1: Proper Materials Selection
The selection of appropriate materials is the first and foremost crucial factor in ensuring quality control of concrete. The right choice of materials impacts the strength and performance of the final concrete product. It is critical to select the materials that meet the required specifications and are suitable for the intended application.
For example, high-strength and durable aggregates, such as quartzite and granite, are well-suited for heavy-duty construction projects, while limestone and lightweight aggregates are suitable for non-structural and decorative applications.
Additionally, it is necessary to consider other factors such as aggregate size, consistency, stability, cement content, and water-cement ratio while selecting the materials. These factors directly influence the workability, strength, and durability of the concrete.
Quality control of concrete ensures that the material selection process is carried out meticulously to achieve the desired quality outcomes. Effective quality control also prevents issues such as poor workability, low strength, and durability that could arise due to improper material selection.


Factor 2: Accurate Proportions and Mixing
When it comes to quality control of concrete, achieving accurate proportions and proper mixing is crucial. Accurate measurements and consistent mixing techniques are necessary for producing high-quality concrete that is strong, durable, and meets the desired outcomes of a project.
Inaccurate proportions may result in weak concrete that is prone to cracking and other structural issues. On the other hand, using the correct proportions with proper mixing techniques ensures that the concrete hardens uniformly, resulting in an even distribution of strength and durability throughout the entire structure.
Consistency in mixing techniques is key to producing high-quality concrete. The concrete mixture should be mixed for an appropriate amount of time for the materials to blend evenly, with additional mixing time depending on the specific type of mix being produced.
The image above exemplifies the importance of accurate proportions and mixing in producing quality concrete. The proper mixture generates a consistent batch of concrete capable of delivering the desired strength and structure, which are essential elements for the success of any construction project.
Conclusion
Quality control of concrete is critical in construction projects, and it directly influences the success and durability of structures. By adhering to strict quality control measures and considering the seven important factors that affect its effectiveness, construction professionals can achieve enhanced structural integrity, improved durability and longevity, consistent performance, cost savings, and regulatory compliance.
Implementing quality control measures and ensuring compliance with industry standards and regulations also helps to avoid potential issues and failures that could result in costly repairs and replacements over time. Therefore, it is essential to prioritize quality control of concrete in construction projects to ensure the long-term performance and sustainability of the structures.
In summary, quality control of concrete brings immense benefits to construction projects. By following proper quality control measures and considering important factors that affect its effectiveness, construction professionals can guarantee that the concrete used in their projects accords with the highest standards of durability, performance, and regulatory compliance.
Also, Read
1000Sqft house construction cost in 2022
Compound wall cost per Rft & Sqft
Basic House Construction Cost in 2022