One of the most critical aspects of construction quality is concrete workability. Achieving optimal workability ensures that the final concrete product meets the intended structural requirements and performs as desired. Measuring workability requires understanding the different tests used to evaluate concrete properties.
This section will provide an overview of the various tests used to measure the workability of concrete. By understanding these tests, builders and engineers can select the right concrete mix and make adjustments to achieve optimal results.
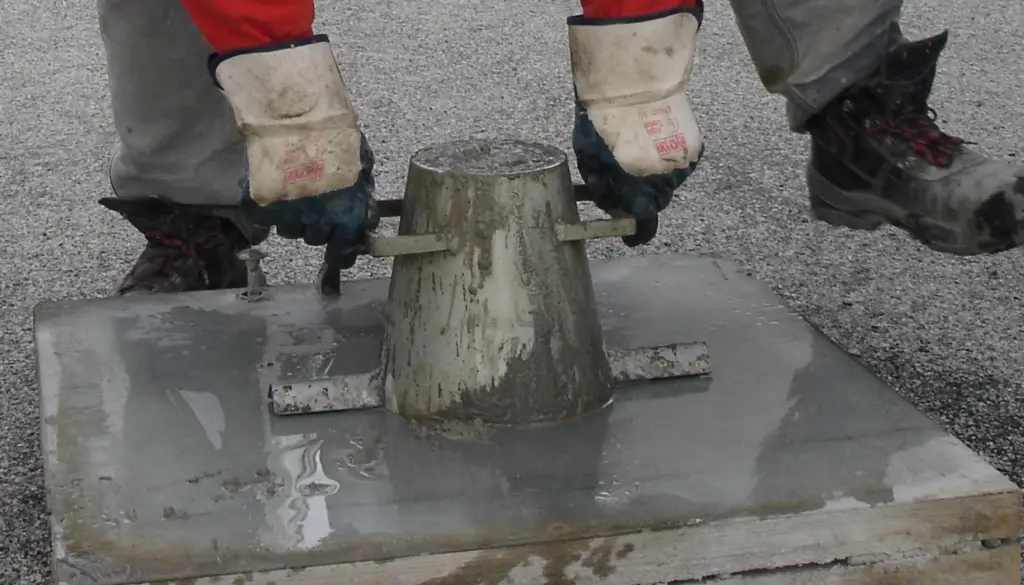
Key Takeaways:
- Measuring workability is essential for achieving optimal construction quality.
- Concrete workability refers to the ease with which the mix can be mixed, placed, compacted, and finished.
- Tests like the slump test, compaction factor test, Vee-Bee test, flow test, and Kelly ball test help measure workability.
- Workability is influenced by factors such as water-cement ratio, aggregate characteristics, and admixtures.
- Following best practices and addressing common workability problems can help achieve the desired results.
What is Concrete Workability?
Before assessing the workability of concrete, it is crucial to understand what it means. Concrete workability refers to the ease with which concrete can be mixed, placed, compacted, and finished. This property is affected by several factors, including the water content, aggregate gradation, and cementitious materials used in the mixture. The degree of workability required for a particular concrete mix depends on the project’s design and the specific construction application.
Assessing workability is an essential part of ensuring high-quality concrete construction. By testing workability, construction professionals can determine whether the concrete mix meets the specific requirements of a given project. Testing concrete workability also helps identify potential issues with the mix before it is too late, maximizing the chances of a successful construction project.
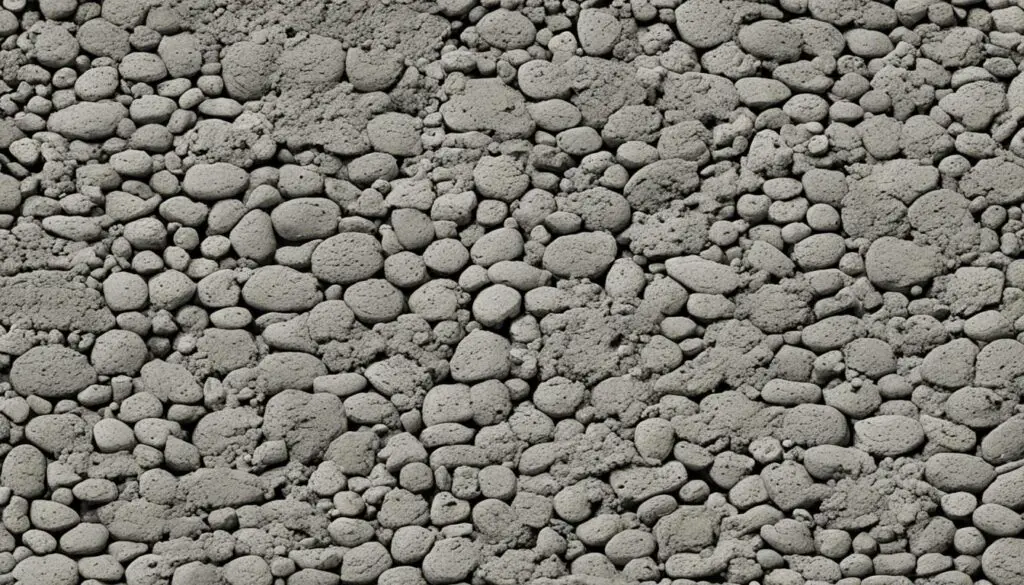
Slump Test: Apparatus, Procedure, and Results
The slump test is a widely used method to determine the workability of fresh concrete. The test measures the consistency or flowability of the concrete, indicating its ability to be placed, compacted, and finished. It is performed using a slump cone and a tamping rod, and the results are interpreted based on the degree of subsidence of the concrete.
The apparatus required for the slump test includes:
- A slump cone with a base diameter of 200 mm, top diameter of 100 mm, and height of 300 mm
- A tamping rod with a diameter of 16 mm and a length of 600 mm
- A non-absorbent base plate
- A measuring scale
- A scoop or trowel
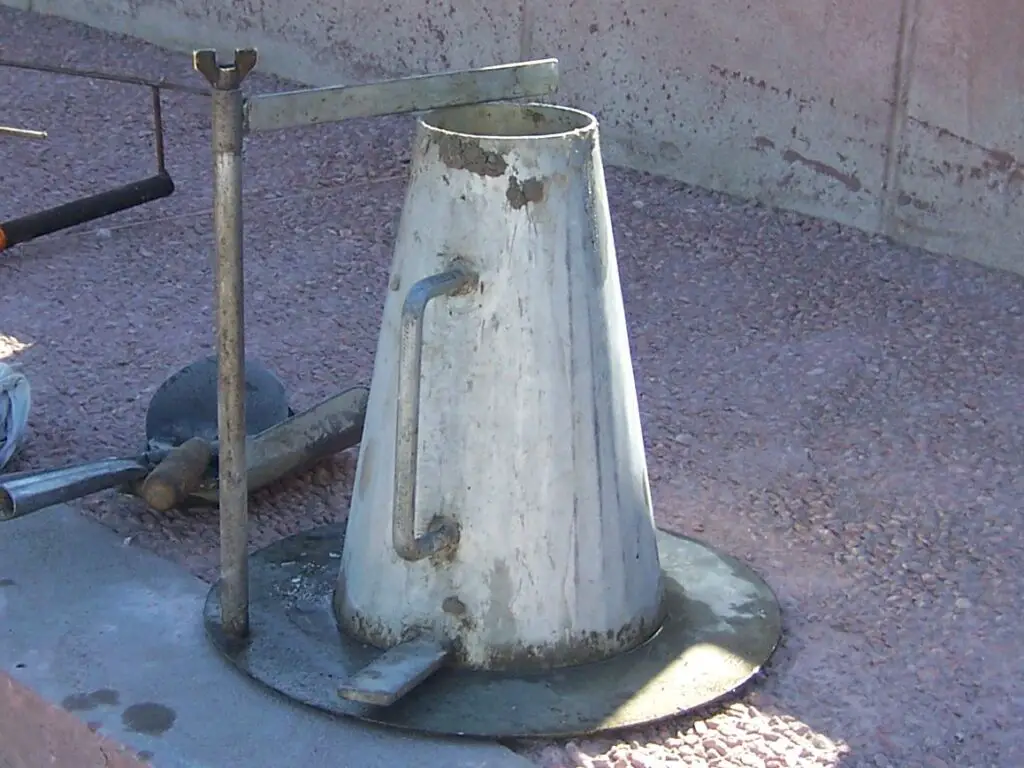
- Thoroughly clean the slump cone and base plate, moisten them with water, and place the cone on the base plate
- Fill the slump cone with fresh concrete in three distinct layers, tamping each layer with 25 strokes of the tamping rod
- Level off the surface of the cone with a trowel or scoop, and mark the point on the tamping rod level with the top of the concrete
- Gently lift the cone vertically and allow the concrete to spread freely and settle
- Measure the subsidence of the concrete from the original height of the cone and record the result as the slump value
The interpretation of the slump test results is usually based on the type of construction planned and the specifications of the project. Generally, a higher slump value indicates a more workable mix, while a lower value signifies a mix that is less workable but tends to be stronger and more durable.
Slump Test Results (mm) | Potential Workability | Common Uses |
---|---|---|
0 – 25 | Very Low | Concrete precast units, pavement slabs, reinforced concrete |
25 – 50 | Low | Mostly used in beams, columns, walls, and heavy construction |
50 – 100 | Medium | General construction, residential construction, slabs, and foundations |
100 -175 | High | Mass concrete works, road construction, and projects where concrete is placed with a pump |
The slump test offers valuable insight into the workability of fresh concrete and helps ensure optimal construction quality. By understanding the required apparatus, following the step-by-step procedure, and interpreting the results correctly, construction professionals can make informed decisions about the best course of action for their specific projects.
Compaction Factor Test: Apparatus and Procedure
The compaction factor test is an essential test that determines the workability of concrete. It measures the compaction of the concrete mix under standard vibration. The compaction factor test provides essential insight into the water-cement ratio and aggregate content of the concrete mix. This test is particularly useful for optimizing the mix design of concrete and determining the most practical and cost-effective solution for a project.
To conduct the compaction factor test, the following apparatus is required:
Apparatus | Quantity |
---|---|
Cylindrical metal Mould | Height: 305mm, Diameter: 100mm |
Compacting machine | Capacity: 200mm/min., Drop: 380mm |
Steel tamping rod | Length: 610mm, Diameter: 16mm |
Weighing machine | Capacity: 500kg, Accuracy: 100g |
The following are the step-by-step procedures for conducting the compaction factor test:
- Take a sample of freshly mixed concrete and fill the cylindrical metal Mould in three layers with equal volume. Each layer should be compacted using 25 strokes of the tamping rod.
- Weigh the cylindrical mold with the compacted concrete to the nearest 10g (W1).
- Empty the mold, clean, and dry it.
- Refill the Mould with the same concrete sample in a single layer. Do not compact it but use the tamping rod to level the surface of the mix.
- Weigh the cylindrical Mould with the uncompacted concrete to the nearest 10g (W2).
- Calculate the compaction factor using the formula: compaction factor = W1/W2.
The compaction factor value ranges between 0.5 to 0.9, where a value closer to 0.9 indicates high workability and a value closer to 0.5 indicates low workability.
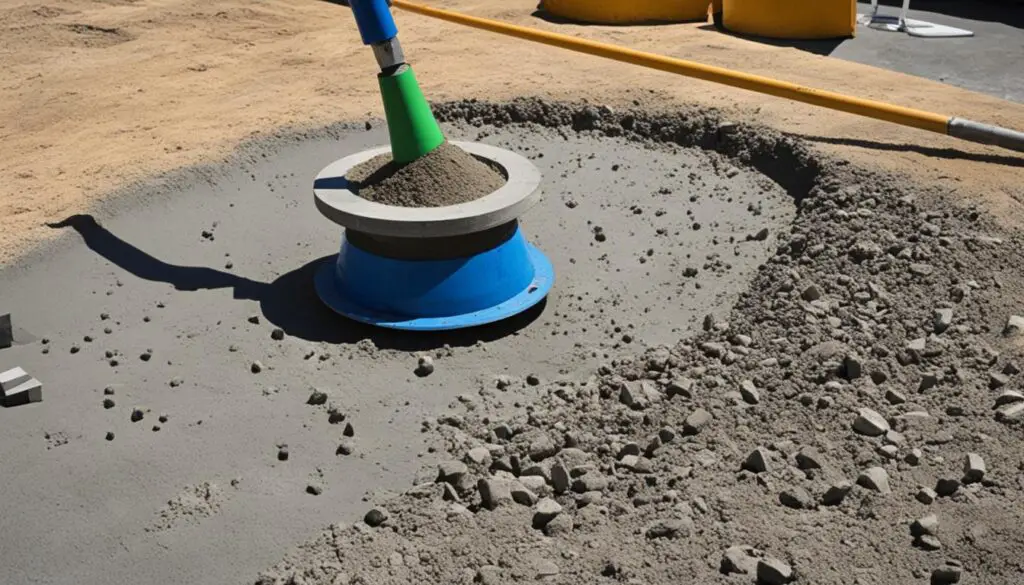
Vee-Bee Test: Apparatus and Procedure
The Vee-Bee test is an essential workability test that measures the concrete’s ability to flow under vibration. The apparatus required for conducting this test includes:
- A vibrating table with dimensions of 400 mm x 400 mm square top and capable of vibrating at a frequency of 3000 (+/- 100) vibrations per minute.
- A standard graduated rod, weighing approximately 50 g, and with dimensions of 16 mm in diameter and 600 mm in length.
- A stainless steel container with dimensions of 200 mm in diameter and 200 mm in height.
- A stopwatch to keep track of the time.
The procedure for conducting the Vee-Bee test involves the following steps:
- Place the stainless steel container on the vibrating table with a damp cloth underneath.
- Fill the container with wet concrete and level it with a trowel.
- Start the vibrating table and maintain it for 60 seconds for concrete of normal consistency and 1.5 minutes for concrete of very low or high consistency.
- After the specified duration, pull out the graduated rod from the concrete, and measure the time taken for the concrete to settle. This time is known as the Vee-Bee time.
The Vee-Bee time indicates the concrete’s workability. A shorter Vee-Bee time indicates a higher workability, while a longer Vee-Bee time indicates a lower workability. This test is particularly useful in determining the workability of concrete mixes used in concrete road pavements, concrete precast elements, and concrete pipes.

Flow Test: Apparatus and Procedure
The flow test is a widely used method to measure the flowability of fresh concrete, and it is also known as the flow cone test or the flow table test. This test helps evaluate the consistency of concrete, and it is essential for ensuring optimal construction quality.
The apparatus required for conducting a flow test includes a slump cone, a scale, a flow table, a tamping rod, and a scoop. To begin the flow test, the slump cone is filled with fresh concrete and lifted away carefully, allowing the concrete to settle naturally. The flow table is then set up with a tamping bar and cone, where the cone is filled with concrete, and is tamped 25 times using the tamping bar. Once the concrete is leveled off, the cone is lifted away, allowing the concrete to spread on the table. The diameter and the average of two perpendicular diameters are then measured to calculate the flow value.
The flow test is a quick, simple, and reliable technique for measuring the flowability of concrete, allowing contractors and engineers to evaluate its workability. Conducting flow tests using this procedure ensures that concrete meets the desired consistency for the intended application.
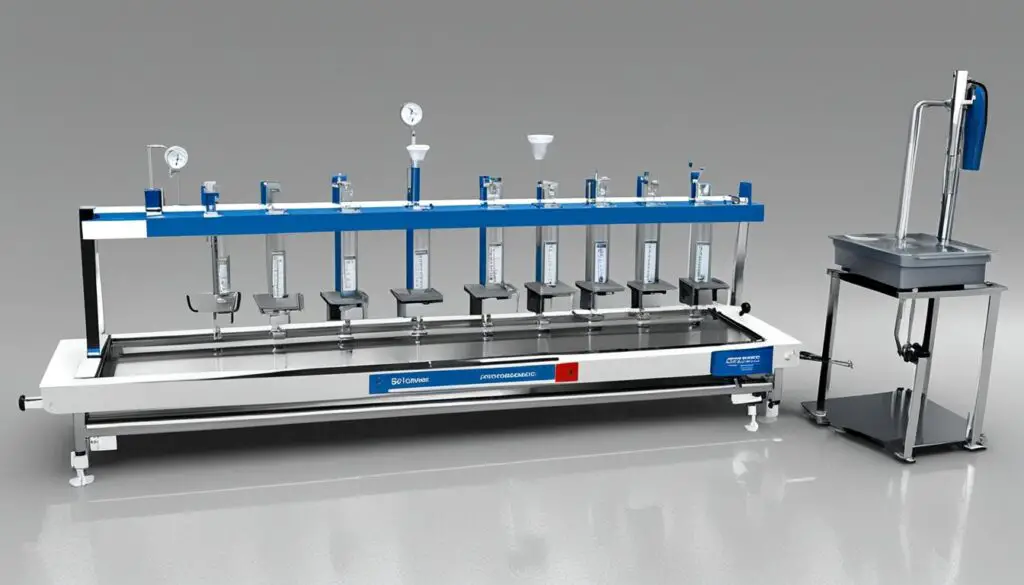
Summary Table: Flow Test Procedure
Step No. | Procedure | Apparatus Required |
---|---|---|
1 | Fill the slump cone with fresh concrete | Slump cone |
2 | Lift the cone away and let the concrete settle naturally | Slump cone and scale |
3 | Set up the flow table with the tamping bar and cone | Flow table, tamping rod, and cone |
4 | Fill the cone with the concrete and tamp it 25 times using the tamping bar | Flow table, tamping rod, and cone |
5 | Lift the cone away and let the concrete spread on the table | Flow table and cone |
6 | Measure the diameter and the average of two perpendicular diameters to calculate the flow value | Scale and measuring instruments |
Kelly Ball Test: Apparatus and Procedure
The Kelly Ball test is an efficient method to measure the workability and consistency of fresh concrete. This test is often used in construction projects to determine the suitability of concrete for various applications. The procedure involves dropping a metal ball into the concrete and measuring the depth of the indentation created by the ball. The depth of indentation is directly proportional to the workability of the concrete.
The Kelly ball test is particularly useful in assessing concrete mixtures with a low slump.
Apparatus
The apparatus required to conduct the Kelly ball test includes:
Apparatus | Specification |
---|---|
Kelly ball | 10-pound (4.54kg) metal ball with a diameter of 3 inches (76mm) |
Scale | Capable of weighing up to 100 pounds (45.36kg) |
Plate or tray | For supporting and holding the fresh concrete during the test |
Measuring rule | For measuring the depth of the indentation |
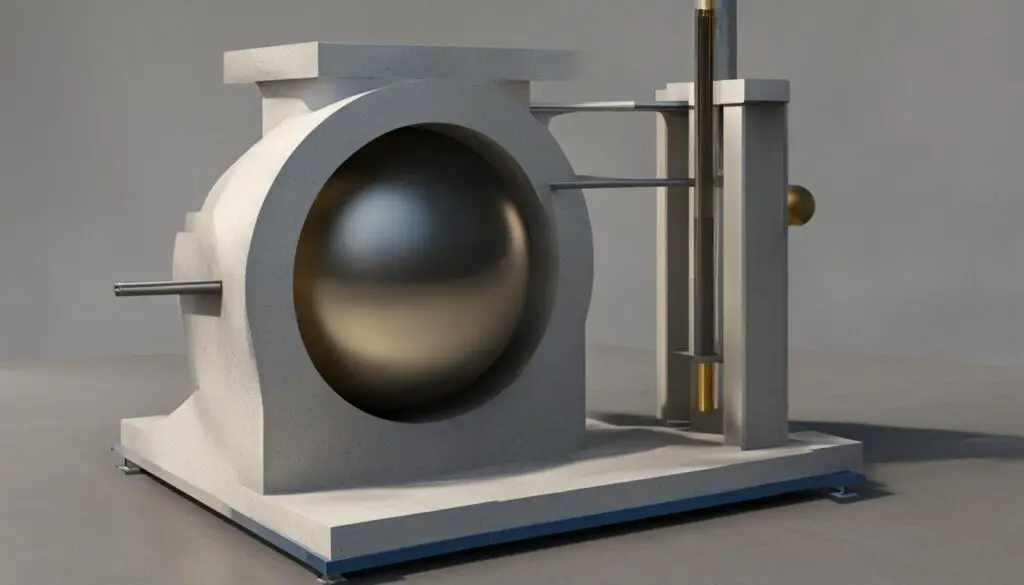
Procedure
The procedure for conducting the Kelly ball test involves the following steps:
- Ensure that the apparatus is clean and dry.
- Pour the fresh concrete into the plate or tray.
- Place the Kelly ball on the surface of the concrete.
- Quickly lift the ball, allowing it to drop and strike the concrete surface.
- Measure the depth of the indentation created by the ball using the measuring rule.
- Record the measurement and repeat the test at least two more times to obtain an average value.
Note that the Kelly ball test is not suitable for concrete mixtures with a slump greater than 4 inches (100mm)
Benefits of the Kelly Ball Test
The Kelly Ball test is a fast and simple way to measure the workability of fresh concrete. It provides valuable insights to ensure that the concrete has the necessary flow properties to allow proper placement, compaction, and finishing. By conducting the Kelly ball test, construction professionals can ensure that their concrete mixtures meet the required workability standards, resulting in high-quality construction projects.
Importance of Concrete Workability Tests
The importance of concrete workability tests cannot be overstated when it comes to ensuring optimal construction quality. These tests help determine the ability of fresh concrete to be mixed, placed, compacted, and finished, which has a direct impact on the properties and performance of the final product.
By conducting concrete workability tests, construction professionals can identify any issues in the mix and adjust it accordingly. This helps ensure that the concrete will meet the necessary strength, durability, and other characteristics required for the project.
Moreover, conducting concrete workability tests can save time and resources in the long run. Identifying issues early on allows for adjustments to be made before significant amounts of concrete are poured, preventing costly rework and delays.
The importance of concrete workability tests cannot be overstated, and every construction project should make use of these tests to ensure optimal results.
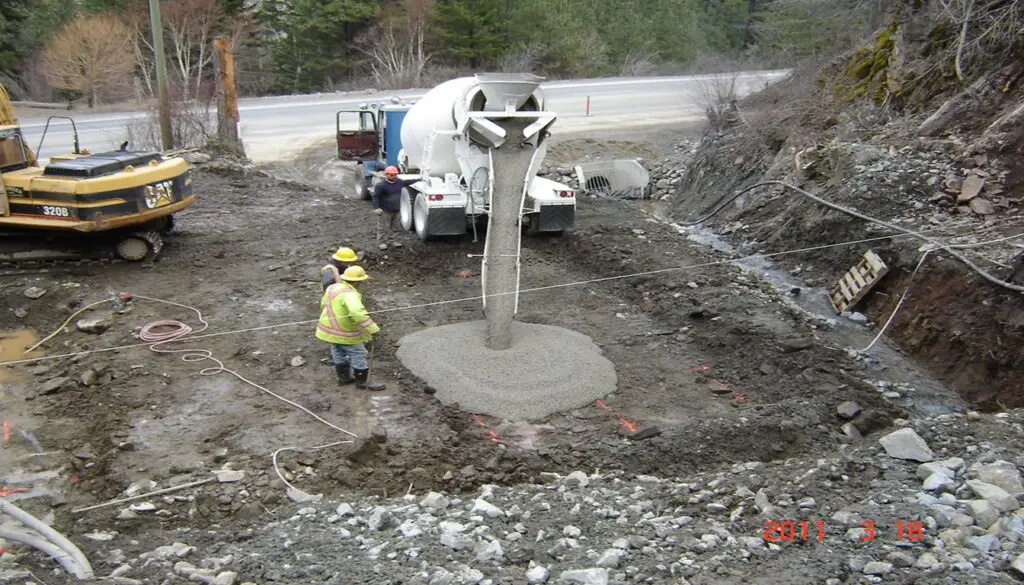
Factors Affecting Concrete Workability
The workability of concrete can be defined as the ease with which it can be mixed, placed, compacted, and finished. Several factors can affect the workability of concrete, making it important to understand and control them to achieve the desired results in construction projects.
One of the primary factors affecting concrete workability is the water-cement ratio. The water-cement ratio determines the amount of water necessary to hydrate the cement. A lower water-cement ratio will result in higher workability, while a higher ratio will reduce workability and increase the potential for shrinkage and cracking.
The characteristics of aggregates such as shape, size, and grading can also significantly impact workability. Angular and elongated aggregates tend to reduce workability by increasing friction and reducing flowability. On the other hand, round and smooth aggregates can enhance workability by improving flowability and reducing friction.
Admixtures and additives can also affect the workability of concrete. For instance, superplasticizers can improve workability by reducing the amount of water needed for a given consistency, while accelerators can decrease workability by speeding up the setting time of the mix.
Understanding and controlling these factors can help construction professionals achieve optimal workability and high-quality concrete results.
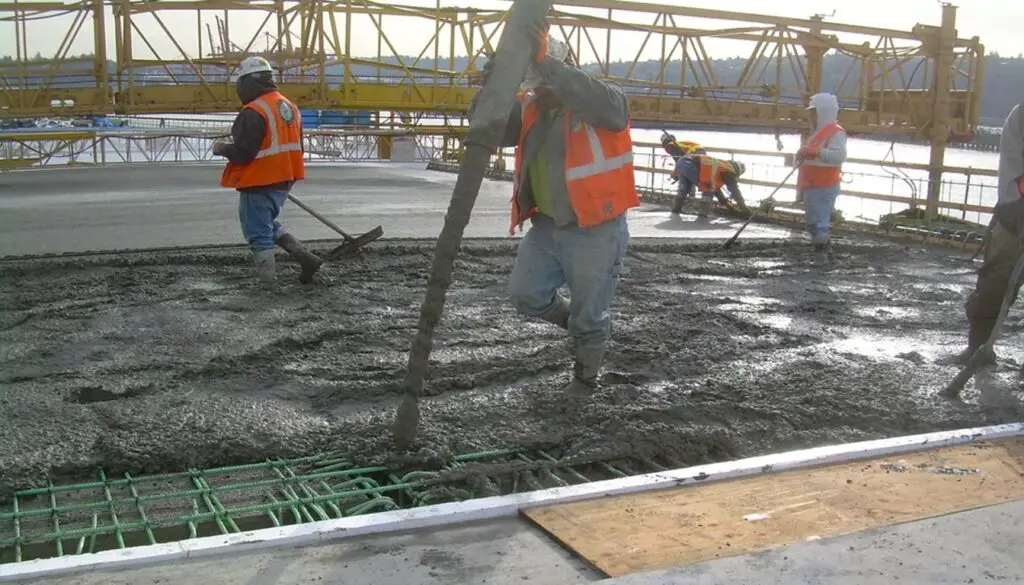
Factors | Effects on Workability |
---|---|
Water-Cement Ratio | A lower ratio enhances workability, while higher ratios decrease workability. |
Aggregate Characteristics | Size, shape, and grading impact workability. Round and smooth aggregates enhance, while angular and elongated aggregates reduce workability. |
Admixtures and Additives | Superplasticizers can improve workability, while accelerators can decrease workability. |
Best Practices for Achieving Optimal Concrete Workability
Concrete workability is crucial for ensuring the successful completion of any construction project in India. Achieving optimal concrete workability requires adherence to specific best practices that enhance concrete mixtures and ensure durability, strength, and overall quality.
Tip 1: Maintain Appropriate Water-Cement Ratio
To achieve the desired workability, it is essential to use a suitable water-cement ratio. This ratio has a significant impact on the concrete’s strength, durability, and workability. The ideal ratio should be between 0.45 and 0.55, depending on the specific requirements of the structure.
Tip 2: Choose Appropriate Aggregates
The choice of aggregates significantly affects the workability of concrete. It is essential to use well-graded aggregates that provide adequate voids for the cement to bind with and create strong, durable concrete. Proper testing and selection of aggregates can ensure the desired workability and overall quality of the concrete mix.
Tip 3: Use High-Quality Admixtures
The use of high-quality admixtures can significantly improve the workability of concrete and provide other beneficial qualities such as increased strength, reduced permeability, and enhanced durability. It is crucial to use admixtures that are compatible with the specific mix design and can withstand the local environment and climate.
Tip 4: Proper Mixing and Placement Techniques
Proper mixing and placement techniques are critical for achieving optimal concrete workability. It is essential to use efficient mixing equipment and techniques that ensure proper distribution of all ingredients throughout the mix. The concrete should also be placed immediately after mixing, using appropriate equipment that enables proper compaction and finishing.
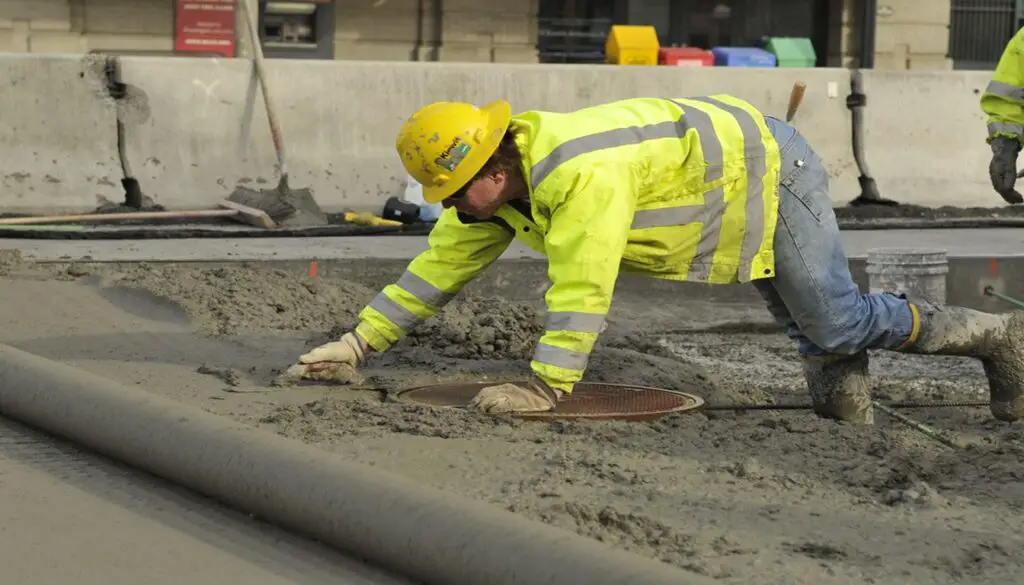
Curing is the process of maintaining moisture and temperature in concrete for a specific period to ensure proper hardening and adequate strength development. Proper curing can significantly enhance the workability of concrete while ensuring durability, strength, and overall quality. It is essential to follow specific curing practices and maintain optimal conditions to enhance concrete workability.
The above tips and guidelines can help construction professionals achieve optimal concrete workability in India. By following these best practices, workers can ensure durable, high-quality concrete that meets the specific requirements of the construction project.
Common Workability Problems and Solutions
Despite the importance of workability in constructing quality concrete, workability problems can still arise. This section will explore some common issues and provide potential solutions to address them effectively.
Problem: Segregation
Segregation occurs when the coarse aggregate in concrete separates from the cement paste. This can result in a non-uniform mix that weakens the final product’s overall strength and durability.
Solution: Use well-graded aggregate with a wide range of particle sizes. Use the minimum amount of water needed to ensure the mix’s workability.
Problem: Bleeding
Bleeding occurs when excess water in the mix rises to the surface and evaporates, leaving behind small voids and cracks. This can reduce the concrete’s strength, durability, and appearance.
Solution: Adjust the aggregate ratios to reduce water demand in the mix and limit the time between mixing, laying, and finishing. Use plasticizers and stabilizers to improve the mix’s cohesion and air-entraining agents to facilitate bleeding prevention.
Problem: Low Slump
A low slump indicates that the mix is too dry. This can make it challenging to pour, place, and finish to achieve the desired shape and appearance.
Solution: Adjust the mix by adding more water, super plasticizers, or stabilizers to increase the slump. Ensure that there is adequate consolidation during the placement process.
Problem: High Slump
A high slump indicates that the mix is too wet and can be difficult to control during placement, resulting in segregation and bleeding.
Solution: Reduce the Water-Cement Ratio (WCR) improves the mix’s workability without increasing the slump. When placing cement that has already reached its setting time, use retarders to delay the hardening process.
By recognizing common workability problems and employing effective solutions, it is possible to achieve optimal concrete workability and construction quality, improving the overall durability and performance of the project.
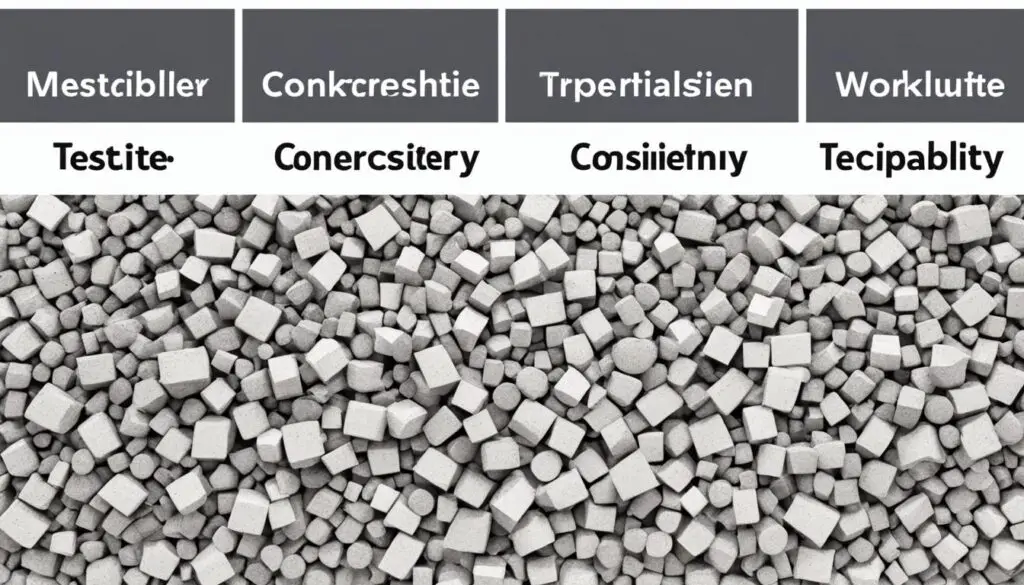
Understanding Workability in the Indian Construction Industry
The Indian construction industry is one of the fastest-growing sectors in the world, with a massive demand for quality infrastructure to support the country’s rapid economic growth. Concrete, being the most widely used construction material, plays a vital role in the industry’s success.
Workability is a critical characteristic of concrete in India’s construction practices, given the diverse environmental and site conditions and the need to optimize resources. The workability of concrete significantly affects the quality and durability of the constructed infrastructure.
In the Indian construction industry, the most commonly used test for measuring concrete workability is the slump test. The test is straightforward and quick, making it the preferred choice for onsite testing. However, it has its limitations and may not accurately measure the workability of all types of concrete mixes.
There are also unique challenges faced by the Indian construction industry in achieving optimal concrete workability, such as the availability and quality of raw materials, labor and skill levels, and weather conditions. The hot and humid climate prevalent in many regions of India can lead to rapid setting of concrete, making it challenging to achieve the desired workability.
To overcome these challenges, Indian contractors often rely on admixtures to improve workability and performance. Admixtures such as plasticizers, retarders, and viscosity modifiers can provide substantial benefits in terms of workability, strength, and durability, and optimize resource utilization.
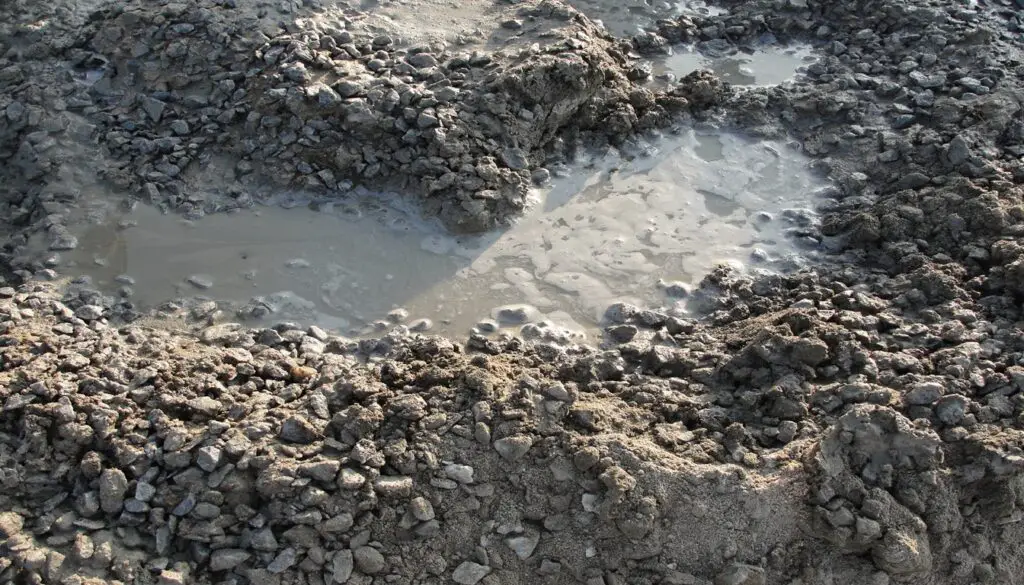
In conclusion, achieving optimal concrete workability is critical to the overall success of the Indian construction industry. Using the right tests, considering unique challenges, and leveraging suitable admixtures can help ensure that the constructed infrastructure is of the desired quality and durability.
Conclusion
In conclusion, the measurement and understanding of concrete workability are key to ensuring optimal construction quality and performance. The slump test, compaction factor test, Vee-Bee test, flow test, and Kelly ball test are effective methods for assessing workability. By following best practices and addressing workability problems, the Indian construction industry can achieve excellent results in concrete workability. This will ultimately lead to a reduction in costs and an improvement in overall construction quality.
Thanks For the Great Attention!
Good Bye & Take Care
Happy Learning
Also, Read,