AAC Blocks Manufacturing Process
AAC (Autoclaved Aerated Concrete) blocks are a popular lightweight, strong, durable, high-performance, and environmentally friendly building material used for construction due to their numerous advantages that are made by mixing fine aggregate, cement, lime, gypsum, aluminum powder, and water.
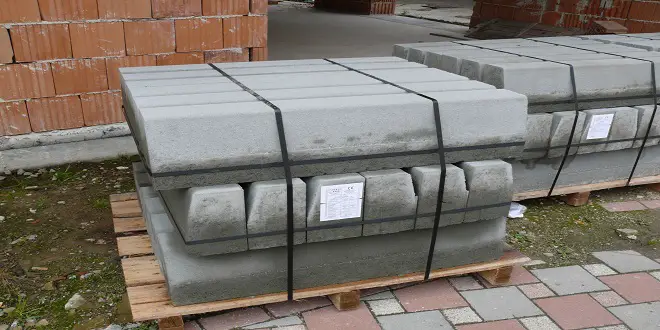
The mixture is then poured into molds where it is allowed to expand and cure, resulting in a cellular structure that is lightweight, strong, and has excellent insulation properties.
The AAC Blocks Manufacturing Process can be divided into the following stages:
1). Raw material preparation
2). Mixing
3). Pouring
4). Curing
5). Cutting
6). Stacking
7). Finishing
Let’s Discuss this in detail
1). Raw material preparation
The raw materials used in AAC Blocks Manufacturing Process are sand or fly ash, cement, lime, gypsum, aluminum powder, and water. The raw materials are first measured and then mixed in the required proportions in a ball mill or a mixer. will discuss each of these raw materials in detail.
1). Sand or Fly Ash
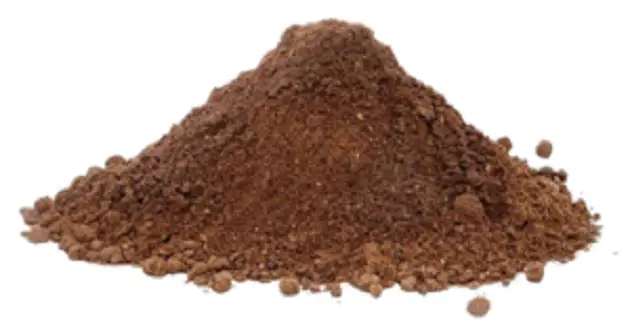
The primary raw material used in the AAC Blocks Manufacturing process is sand or fly ash. Sand is a naturally occurring granular material composed of finely divided rock and mineral particles. Fly ash, on the other hand, is a fine, glass-like powder recovered from the gases of burning coal. Both materials are used as a fine aggregate in AAC block production.
The sand or fly ash used in AAC Blocks Manufacturing Process should be free from impurities, including clay, silt, organic matter, and salts. The sand should also be well-graded, with a particle size distribution that allows for good workability and compaction.
2). Cement
Cement is the binder used in AAC Blocks Manufacturing Process. The type of cement used in AAC block production is typically Portland cement.
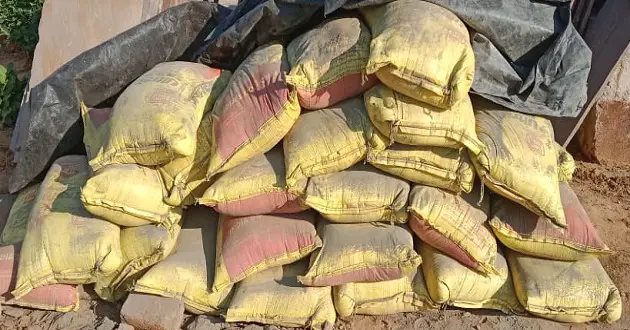
It is a fine powder made from a mixture of limestone, clay, and other minerals that are heated in a kiln and then ground to a fine powder. Cement binds the raw materials together, providing strength and durability to the final product.
3). Lime
Lime is a fine powder made from heating limestone to high temperatures.
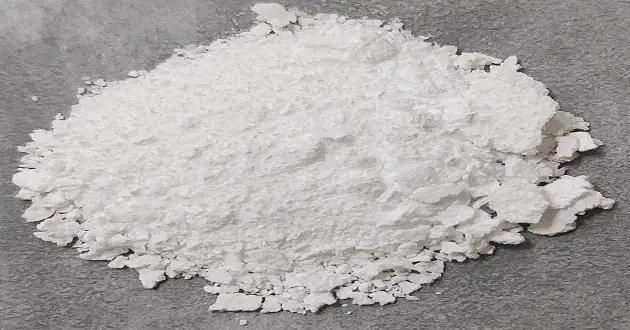
It is used in AAC block production as a mineral additive to improve the workability and strength of the blocks. Lime also helps to reduce the shrinkage and cracking of the blocks during the curing process.
There are two types of lime used in AAC block production: quicklime and hydrated lime.
Quicklime is made by heating limestone in a kiln to very high temperatures.
Hydrated lime is made by adding water to quicklime, causing a chemical reaction that produces a fine powder.
4). Gypsum
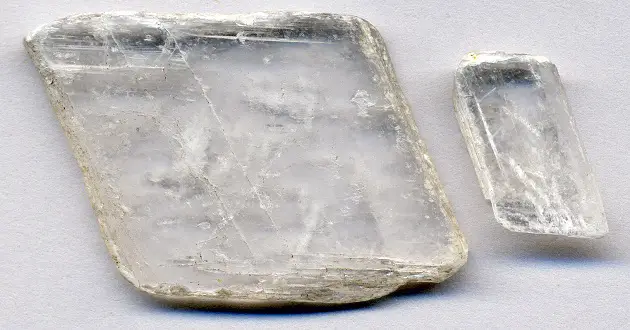
Gypsum is a soft, white mineral that is commonly used in construction as a binder and a filler. It is added to the raw materials used in AAC block production to improve the workability and set time of the mixture. Gypsum also helps to reduce the shrinkage and cracking of the blocks during the curing process.
5). Aluminum Powder
Aluminum powder is a fine powder made from aluminum metal.
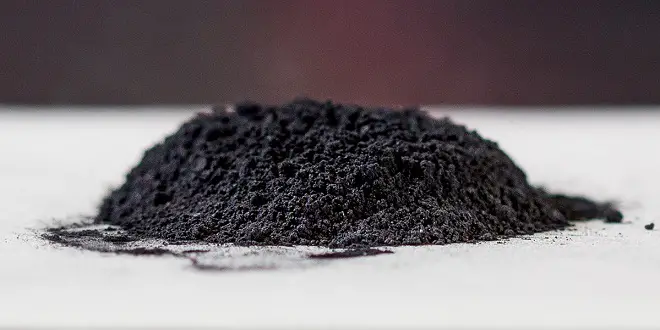
It is added to the slurry mixture used in AAC block production to create air bubbles in the mixture. These air bubbles expand during the curing process, creating the cellular structure of the AAC blocks. The use of aluminum powder also helps to improve the insulation properties of the blocks.
6). Water
Water is an essential component in AAC block production. It is added to the raw materials to create a slurry mixture that is poured into molds to form the blocks. The water used in AAC block production should be clean and free from impurities such as salts, acids, and alkalis.
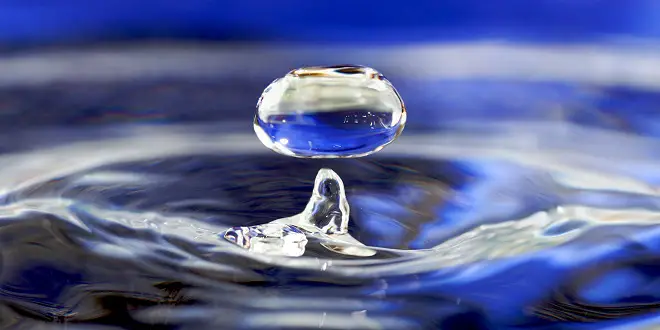
The amount of water added to the mixture is critical as it affects the workability and strength of the blocks. Too much water can result in weak blocks, while too little water can make the mixture difficult to pour and compact.
Note:-
AAC blocks are made from a combination of sand or fly ash, cement, lime, gypsum, aluminum powder, and water. Each of these raw materials plays a critical role in the AAC Blocks Manufacturing Process, contributing to the strength, durability, and insulation properties of the blocks. By understanding the properties and characteristics of each of these raw materials, manufacturers can produce high-quality AAC blocks that meet the needs of the construction industry.
2). Mixing
The mixing process is an essential stage in AAC Blocks Manufacturing Process.
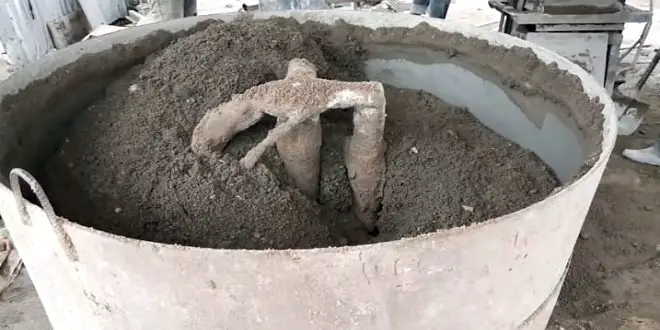
The process involves mixing the raw materials, including sand or fly ash, cement, lime, gypsum, aluminum powder, and water, in the correct proportions to produce a slurry that will form the basis of the AAC blocks. Now we will discuss the mixing process of AAC block manufacturing.
1). Measuring the Raw Materials
The first step in the mixing process is to measure the raw materials accurately. Each raw material is weighed separately and recorded to ensure that the correct proportions are used.
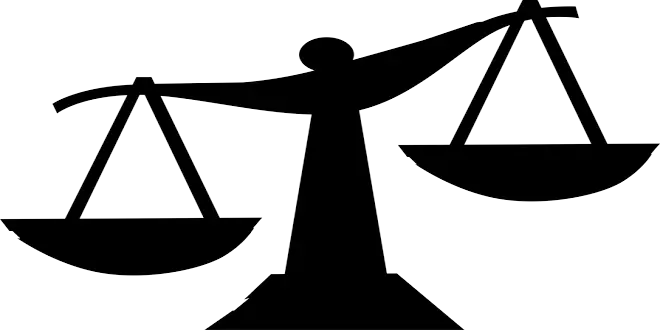
The measurements are critical as the quality of the final product is determined by the precise ratio of the raw materials used.
2). Mixing the Raw Materials
Once the raw materials have been measured, they are mixed together in a mixing drum or reactor. The mixer used for AAC block production is a horizontal or vertical paddle mixer. The mixer should be capable of producing a homogenous mixture that ensures that each particle of the raw materials is uniformly distributed.
The mixing process should be carried out for a specific period to ensure that the mixture is uniformly blended. The mixing time can vary depending on the size and capacity of the mixer used. It typically takes between 5 to 15 minutes for the mixer to produce a uniform slurry.
3). Adding Aluminum Powder
Once the raw materials have been mixed, the next step is to add the aluminum powder. The aluminum powder is added to the slurry in a separate tank. The aluminum powder reacts with the slurry to produce hydrogen gas, which generates bubbles in the slurry. These bubbles create a cellular structure in the AAC blocks.
The aluminum powder should be added to the slurry in the correct proportion. The amount of aluminum powder used can vary depending on the desired density and strength of the AAC blocks.
4). Mixing the Slurry and Aluminum Powder
After the aluminum powder has been added, the slurry and aluminum powder are mixed together in a separate mixer for a specific period. The mixing time should be controlled to ensure that the mixture is uniformly blended and that the aluminum powder is evenly distributed throughout the slurry.
During the mixing process, the slurry and aluminum powder are blended to form a homogenous mixture. The mixture should be of a specific consistency and viscosity to ensure that it can be poured into the molds easily.
Note:-
The mixing process is an essential stage in the AAC Blocks Manufacturing Process. The process involves measuring the raw materials, mixing them in the correct proportions, adding the aluminum powder, and then mixing the slurry and aluminum powder together to form a homogenous mixture. The mixing process should be carefully controlled to ensure that the mixture is uniformly blended and that the AAC blocks produced meet the required strength and density requirements.
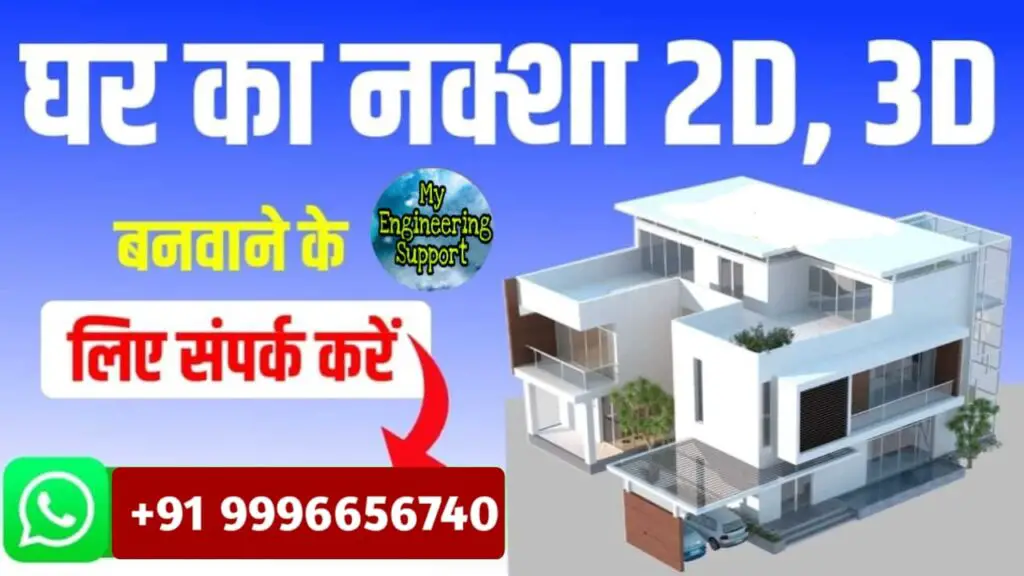
3). Pouring
The pouring process is a critical stage in the AAC Blocks Manufacturing Process or production of Autoclaved Aerated Concrete (AAC) blocks. The process involves pouring the mixed slurry into molds and allowing it to settle and expand. let’s discuss the pouring process of AAC block manufacturing in detail.
1). Preparation of Molds
The first step in the pouring process is the preparation of the molds. The molds used for AAC block production are usually made of steel or wood. The molds are designed to give the AAC blocks their desired shape and size.
Before pouring the slurry into the molds, the molds are treated with a release agent to prevent the blocks from sticking to the molds. The release agent is a chemical that forms a film on the surface of the molds, making it easier to remove the blocks once they are cured.
2). Pouring the Slurry
Once the molds are prepared, the mixed slurry is poured into them. The slurry is poured into the molds up to a specific height, depending on the desired thickness of the blocks. The slurry is poured gently to avoid disturbing the bubbles created by the aluminum powder, which forms the cellular structure of the blocks.
The pouring of the slurry should be carried out carefully to avoid creating air pockets or gaps in the mixture. The pouring process should be completed quickly to ensure that the slurry does not begin to set before it is poured into the molds.
3). Allowing the Slurry to Settle
Once the slurry has been poured into the molds, it is allowed to settle for a specific period. During this period, the slurry begins to solidify, and the bubbles created by the aluminum powder start to expand. The settling time can vary depending on the size and thickness of the blocks being produced. Typically, the settling time can be between 1 and 4 hours.
4). Removing Air Pockets
During the settling period, it is essential to check the slurry for air pockets or gaps. If air pockets are present, they can lead to weak spots in the blocks. To remove any air pockets, the molds are tapped gently to ensure that the slurry settles and fills any gaps.
5). Demolding the Blocks
After the settling period, the AAC blocks are removed from the molds. The blocks are removed carefully to avoid damaging them. The blocks are usually still soft at this stage and require further curing before they can be cut and finished.
Important Note:-
The pouring process is an essential stage in the AAC Blocks Manufacturing Process. The process involves pouring the mixed slurry into molds, allowing it to settle, removing any air pockets, and demolding the blocks. The pouring process should be carried out carefully to ensure that the AAC blocks produced meet the required strength and density requirements.
4). Curing
Once the AAC blocks have been removed from the molds, they are cured in an autoclave or curing chamber. Here, the blocks are cured by subjecting them to high-pressure steam and temperature. This process activates the aluminum powder, which creates additional gas and expands the cells in the block.
This process takes several hours, depending on the size and thickness of the blocks being produced. Typically, the curing time can be between 8 to 12 hours. The curing process allows the blocks to gain their strength and hardness.
5). Cutting
After the AAC blocks have been cured, they are removed from the autoclave or curing chamber and transported to the cutting machine. The cutting machine is a specialized piece of equipment designed to cut the AAC blocks into the desired size and shape.
The cutting machine uses a wire or a blade to cut the blocks. The wire or blade is guided by a computer-controlled system that ensures the blocks are cut accurately and uniformly.
The cutting process produces a lot of dust and debris, which must be carefully managed to prevent it from contaminating the environment. To minimize the impact of dust and debris, the cutting machine is usually fitted with a dust collection system.
Related Video
AAC Blocks Manufacturing Process
6). Stacking
After the AAC blocks have been cut, they are stacked on pallets or shelves. The blocks are stacked carefully to ensure that they do not become damaged or cracked.
The stacking process is critical as it determines the quality and appearance of the finished product. The blocks should be stacked in a uniform and consistent manner, with the edges and corners aligned correctly.
7). Finishing
The finishing process is the final stage in the AAC Blocks Manufacturing Process. The finishing process involves sanding or painting the blocks, to give them a smooth finish and enhance their appearance.
The finishing process can vary depending on the desired appearance of the blocks.
1). Sanding
It is a process that involves using a sanding machine to smooth the surface of the blocks. The sanding process removes any rough edges or bumps and gives the blocks a smooth and uniform appearance.
2). Painting
It is a process that involves applying a coat of paint to the surface of the blocks. The paint used is usually water-based paint that is designed to adhere to the surface of the blocks. The paint gives the blocks a uniform appearance and protects them from the weather.
Conclusion,
The AAC block manufacturing process is a highly controlled and precise process that involves several stages, including raw material preparation, mixing, pouring, curing, cutting, and finishing. The result is a lightweight, strong, and highly insulating building material that is widely used in the construction industry.
Thank you for taking the time to read this educational blog post about the AAC Blocks Manufacturing Process. We hope that you found it informative and engaging. If you have any questions or comments, please feel free to leave comments in the comment section below. Don’t forget to check out our other educational posts on myengineeringsupport.com for more learning opportunities!
Bar Bending Schedule (BBS) Basics Part -1
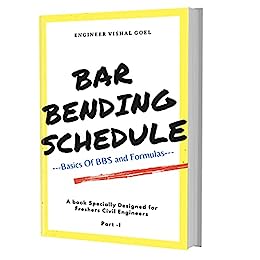
This Ebook is specially designed for Freshers Civil Engineers. Recommended for Quantity Surveyors & Billing Engineers. Here You Can Learn All Basic Concepts & Formulas for Bar Bending schedules (BBS).
I hope this information can be useful for you guys.
If you like this article then please share it with your friends & also like our Facebook Page and join our Telegram Channel.
If you want a PDF copy of this, Do let’s know by commenting & you can message us on our Instagram & telegram channel, or you can download it from the top right-hand corner of this post.
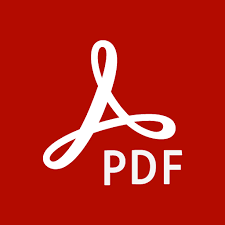
Thanks For the Great Attention!
Good Bye & Take Care
Happy Learning
Also, Read,
28 Important Comparison between WPC and PVC Wall Panel
MDF VS Particle Board – 15 Important Differences
Flush Door vs Wooden Panel Door
UPVC vs Aluminium vs Wooden Windows
Related Video-
“Thank you for the info! We’re a AAC Block Plant Manufacturers too. Check our website at Buildmate