AAC Block Quality Checklist
AAC blocks, also known as Autoclaved Aerated Concrete blocks, are a type of lightweight concrete block made of natural raw materials like cement, sand, water, and gypsum. They are an eco-friendly and sustainable option for construction, as they require less energy and resources to produce, have excellent insulation properties, and are resistant to fire and pests.
However, it is essential to ensure the quality of AAC blocks before using them in construction to avoid any safety or durability issues. In this article, we will discuss in detail how to check the quality of AAC blocks.
The AAC block quality checklist can be divided into the following stages:
1). Visual inspection
2). Density
3). Compressive strength
4). Sound insulation
5). Thermal conductivity
6). Water absorption
7). Efflorescence
8). Fire resistance
9). Dimensional accuracy:
10). Durability
Let’s Discuss this in detail AAC block quality checklist
1). Visual Inspection
The first step in checking the quality of AAC blocks is a visual inspection. It involves a thorough examination of the blocks for any physical defects or irregularities. The blocks should have a uniform shape and size, and their edges should be straight and clean. The surface should be smooth and free from any cracks, chips, or other defects. Any block with visible cracks, chips, or deformities should be rejected.
Visual inspection is a quick and easy way to identify any issues with the blocks before using them in construction
In this section, we will discuss the various aspects of visual inspection of AAC blocks in detail.
1). Shape and size
The blocks should have a uniform shape and size. The edges should be straight and clean, and the surface should be smooth. The blocks should be free from any cracks, chips, or other defects. Any block with visible cracks, chips, or deformities should be rejected.
2). Surface texture
The surface of the block should be smooth and free from any blemishes. The texture of the block should be consistent throughout. Any block with an uneven or rough surface should be rejected.
3). Color
The color of the blocks should be uniform and consistent. Any variation in color may indicate a difference in the quality of raw materials used in the manufacturing process.
3). Cracking
Any visible cracks on the surface or interior of the block should be rejected as it can lead to reduced strength and durability.
4). Shape irregularities
Any irregularities in the shape or size of the block can lead to improper alignment and fitting during construction, resulting in weaker walls or structures.
5). Surface defects
Surface defects such as chips, dents, or uneven surfaces can affect the overall appearance of the structure and reduce its aesthetic appeal.
6). Moisture content
Moisture content can affect the overall strength and durability of the block. The blocks should be free from any moisture or dampness, which can lead to cracking or warping during the drying process.
2). Density
The density of AAC blocks is an essential factor in determining their strength, durability, and insulation properties. It is crucial to check the density of AAC blocks during quality control to ensure that the blocks meet the required specifications for their intended use.
Let’s See the procedure
i). Sampling
The first step in density inspection is sampling. Samples should be randomly selected from the batch of AAC blocks to ensure that the testing is representative of the entire batch.
ii). Measuring dimensions
The length, width, and height of each block should be measured using a digital caliper or ruler to determine the volume of the block. The dimensions should be measured at three different points, and the average value should be taken.
iii). Weighing the block
The block should be weighed using a digital weighing scale to determine its mass. The weighing scale should have a precision of at least 0.1 grams.
iv). Calculation of density
The density of the block can be calculated by dividing the mass of the block by its volume. The formula for calculating the density of the block is:
Density = Mass (in kg) / Volume (in m3)
iv). Comparison with standards
The density of AAC blocks should be between 550 to 650 kg/m3. The measured density of the block should be compared with the required standards to determine if it meets the required specifications.
v). Identification of blocks with low density
If the measured density of the block is lower than the required standard, it indicates that the block may not have the required strength or insulation properties. Blocks with low density should be rejected and not used in construction.
vi). Identification of blocks with high density
If the measured density of the block is higher than the required standard, it indicates that the block may not have the desired insulation properties. Blocks with high density can be used in construction, but their insulation properties may not be as effective as blocks with the desired density.
vii). Repeat the test
In case of any doubts, the test should be repeated on a new sample of blocks to ensure that the results are accurate and consistent.
viii). Record keeping
The results of the density inspection should be recorded and maintained for future reference. This will help in tracking the quality of the blocks over time and identifying any trends or issues.
The density of AAC blocks is a crucial factor in determining their strength and durability. The density of AAC blocks should be between 550 to 650 kg/m3. A block with a density lower than 550 kg/m3 may not have the required strength, while a block with a density higher than 650 kg/m3 may not have the desired insulation properties.
Density inspection is an essential part of quality control or AAC block quality checklist. It is crucial to ensure that the blocks meet the required density specifications to ensure their strength, durability, and insulation properties. Any block with low density should be rejected, while blocks with high density can be used but may not provide the desired insulation properties. Accurate and consistent testing, record-keeping, and attention to detail are crucial for the successful density inspection of AAC blocks.
3). Compressive Strength
Compressive strength is one of the most important parameters for determining the quality and durability of AAC blocks. Compressive strength is the maximum load that a block can bear without breaking under compression. It is crucial to check the compressive strength of AAC blocks during quality control to ensure that the blocks meet the required specifications for their intended use.
In this section, we will discuss the detailed process of compressive strength inspection of AAC blocks.
i). Sampling
The first step in compressive strength inspection is sampling. Samples should be randomly selected from the batch of AAC blocks to ensure that the testing is representative of the entire batch.
ii). Preparation of test specimens
The samples should be cut to prepare test specimens with a size of 150mm x 150mm x 150mm or 100mm x 100mm x 100mm using a diamond saw. The surface of the test specimens should be smooth and free from any defects or irregularities.
iii). Curing
The test specimens should be cured in a water tank or curing chamber for a minimum of 24 hours to ensure that they are fully hydrated and have achieved their maximum strength.
iv). Testing machine
The compressive strength of the test specimens should be measured using a compression testing machine. The testing machine should have a capacity of at least 2000 kN and should comply with the relevant standards.
v). Placing the specimen
The test specimen should be placed on the base plate of the testing machine, and the load should be applied uniformly and steadily until the block fails.
vi). Calculation of compressive strength
The compressive strength of the block can be calculated by dividing the maximum load that the block can bear by its cross-sectional area. The formula for calculating the compressive strength of the block is:
Compressive strength = Maximum load (in N) / Cross-sectional area (in mm2)
vii). Comparison with standards
The compressive strength of AAC blocks should be above 3 N/mm2. The measured compressive strength of the block should be compared with the required standards to determine if it meets the required specifications.
viii). Identification of blocks with low compressive strength
If the measured compressive strength of the block is lower than the required standard, it indicates that the block may not have the required strength and durability. Blocks with low compressive strength should be rejected and not used in construction.
ix). Repeat the test
In case of any doubts, the test should be repeated on a new sample of blocks to ensure that the results are accurate and consistent.
x). Record keeping
The results of the compressive strength inspection should be recorded and maintained for future reference. This will help in tracking the quality of the blocks over time and identifying any trends or issues.
The compressive strength of AAC blocks should be above 3 N/mm2. Any block with a compressive strength lower than 3 N/mm2 should be rejected.
Compressive strength inspection is an essential part of the AAC block quality checklist. It is crucial to ensure that the blocks meet the required compressive strength specifications to ensure their strength and durability. Any block with low compressive strength should be rejected, while blocks with high compressive strength can be used with confidence. Accurate and consistent testing, record-keeping, and attention to detail are crucial for successful compressive strength inspection of AAC blocks.
4). Sound Insulation
Sound insulation is an essential property of AAC blocks, making them ideal for use in constructions that require high levels of soundproofing. It is crucial to check the sound insulation quality of AAC blocks during quality control to ensure that the blocks meet the required specifications for their intended use.
AAC blocks are known for their excellent sound insulation properties. To check the sound insulation quality of AAC blocks, a sound transmission test can be conducted. In this test, the sound is transmitted through the block, and the level of noise reduction is measured. The higher the noise reduction, the better the sound insulation quality of the block.
In this section, we will discuss the detailed process of sound insulation inspection of AAC blocks.
i). Sampling
The first step in sound insulation inspection is sampling. Samples should be randomly selected from the batch of AAC blocks to ensure that the testing is representative of the entire batch.
Testing Apparatus
The sound insulation quality of AAC blocks can be measured using a sound transmission test. The testing apparatus consists of a speaker, an amplifier, a sound level meter, and two test chambers.
ii). Testing procedure
The test specimens should be placed in the test chambers, and the speaker should be placed in the source chamber. The amplifier should be used to produce a specific sound frequency, which is transmitted through the specimen to the receiving chamber. The sound level meter is used to measure the noise reduction achieved by the block.
iii). Noise reduction coefficient (NRC)
The noise reduction coefficient (NRC) is a measure of the sound absorption capacity of a material. The NRC of AAC blocks should be above 0.5. The measured NRC of the block should be compared with the required standards to determine if it meets the required specifications.
iv). Comparison with standards
The measured sound insulation quality of the block should be compared with the required standards to determine if it meets the required specifications.
v). Identification of blocks with low sound insulation quality
If the measured sound insulation quality of the block is lower than the required standard, it indicates that the block may not have the desired soundproofing properties. Blocks with low sound insulation quality should be rejected and not used in constructions that require high levels of soundproofing.
vi). Repeat the test
In case of any doubts, the test should be repeated on a new sample of blocks to ensure that the results are accurate and consistent.
vii). Record keeping
The results of the sound insulation inspection should be recorded and maintained for future reference. This will help in tracking the quality of the blocks over time and identifying any trends or issues.
Sound insulation inspection is an essential part of quality control for AAC blocks. It is crucial to ensure that the blocks meet the required sound insulation specifications to ensure their suitability for constructions that require high levels of soundproofing. Any block with low sound insulation quality should be rejected, while blocks with high sound insulation quality can be used with confidence.
Accurate and consistent testing, record-keeping, and attention to detail are crucial for successful sound insulation inspection of AAC blocks.
5). Thermal Conductivity
Thermal conductivity is an important property of AAC blocks, making them ideal for use in constructions that require high levels of insulation. It is crucial to check the thermal conductivity of AAC blocks during quality control to ensure that the blocks meet the required specifications for their intended use.
In this section, we will discuss the detailed process of thermal conductivity inspection of AAC blocks.
i). Sampling
The first step in thermal conductivity inspection is sampling. Samples should be randomly selected from the batch of AAC blocks to ensure that the testing is representative of the entire batch.
ii). Testing Apparatus
The thermal conductivity of AAC blocks can be measured using a thermal conductivity meter. The testing apparatus consists of a sensor, a heating element, and a temperature-measuring device.
iii). Testing procedure
The test specimens should be placed in the testing apparatus, and the sensor should be placed at the center of the block. The heating element is then used to heat one side of the block, and the temperature measuring device is used to measure the temperature on both sides of the block.
iv). Calculation of thermal conductivity
The thermal conductivity of the block can be calculated using the following formula:
Thermal conductivity = Heat flow (in W/mK) / (Temperature difference x Thickness)
v). Comparison with standards
The thermal conductivity of AAC blocks should be below 0.22 W/mK. The measured thermal conductivity of the block should be compared with the required standards to determine if it meets the required specifications.
vi). Identification of blocks with high thermal conductivity
If the measured thermal conductivity of the block is higher than the required standard, it indicates that the block may not have the desired insulation properties. Blocks with high thermal conductivity should be rejected and not used in constructions that require high levels of insulation.
vii). Repeat the test
In case of any doubts, the test should be repeated on a new sample of blocks to ensure that the results are accurate and consistent.
viii). Record keeping
The results of the thermal conductivity inspection should be recorded and maintained for future reference. This will help in tracking the quality of the blocks over time and identifying any trends or issues.
The thermal conductivity of AAC blocks is another crucial factor in determining their insulation properties. The thermal conductivity of AAC blocks should be between 0.14 to 0.18 W/mK. A block with a higher thermal conductivity value will allow more heat to pass through it, reducing its insulation properties.
Any block with high thermal conductivity should be rejected, while blocks with low thermal conductivity can be used with confidence. Accurate and consistent testing, record-keeping, and attention to detail are crucial for the successful thermal conductivity inspection of AAC blocks.
6). Water Absorption
Water absorption is an important property of AAC blocks, making them suitable for use in construction in humid and coastal areas. It is crucial to check the water absorption of AAC blocks during quality control to ensure that the blocks meet the required specifications for their intended use.
In this section, we will discuss the detailed process of water absorption inspection of AAC blocks.
i). Sampling
The first step in water absorption inspection is sampling. Samples should be randomly selected from the batch of AAC blocks to ensure that the testing is representative of the entire batch.
ii). Weighing the block
The weight of the dry block should be recorded using a digital weighing scale with a precision of at least 0.1 grams.
iii). Soaking the block
The dry block should be soaked in water for a period of 24 hours.
iv). Weighing the soaked block
After 24 hours of soaking, the block should be removed from the water and any excess water should be wiped off with a towel. The weight of the soaked block should be recorded using the same weighing scale used for the dry block.
v). Calculation of water absorption
The water absorption of the block can be calculated using the following formula:
Water absorption = (Weight of soaked block – Weight of dry block) / Weight of dry block x 100
vi). Comparison with standards
The water absorption of AAC blocks should be less than 10% of their weight. The measured water absorption of the block should be compared with the required standards to determine if it meets the required specifications.
vii). Identification of blocks with high water absorption
If the measured water absorption of the block is higher than the required standard, it indicates that the block may not have the desired water resistance properties. Blocks with high water absorption should be rejected and not used in constructions in humid and coastal areas.
viii). Repeat the test
In case of any doubts, the test should be repeated on a new sample of blocks to ensure that the results are accurate and consistent.
ix). Record keeping
The results of the water absorption inspection should be recorded and maintained for future reference. This will help in tracking the quality of the blocks over time and identifying any trends or issues.
AAC blocks are known for their low water absorption properties, making them ideal for construction in humid and coastal areas. The water absorption of AAC blocks should be less than 10% of their weight. Any block with high water absorption should be rejected, while blocks with low water absorption can be used with confidence.
Accurate and consistent testing, record-keeping, and attention to detail are crucial for successful water absorption inspection of AAC blocks.
7). Efflorescence
Efflorescence is a common problem in AAC blocks, and it can lead to a deterioration in their quality and appearance. It is crucial to check the efflorescence of AAC blocks during quality control to ensure that the blocks meet the required specifications for their intended use.
Efflorescence is the white powdery substance that appears on the surface of concrete or masonry due to the presence of salts. To check the efflorescence of AAC blocks, a visual inspection can be conducted. If there is any white powdery substance on the surface of the block, it indicates the presence of salts and should be rejected.
In this section, we will discuss the detailed process of efflorescence inspection of AAC blocks.
i). Sampling
The first step in efflorescence inspection is sampling. Samples should be randomly selected from the batch of AAC blocks to ensure that the testing is representative of the entire batch.
ii). Preparation of test specimens
The samples should be cut to prepare test specimens with a size of 100mm x 100mm x 25mm using a diamond saw. The surface of the test specimens should be smooth and free from any defects or irregularities.
iii). Soaking the block
The test specimens should be soaked in water for a period of 48 hours.
iv). Drying the block
After 48 hours of soaking, the test specimens should be removed from the water and allowed to air dry for a period of 72 hours.
v). Observation
The test specimens should be observed for the presence of efflorescence. Efflorescence is a white, powdery substance that appears on the surface of the block when moisture seeps through the surface and evaporates, leaving behind salts.
vi). Comparison with standards
The presence of efflorescence on AAC blocks is not acceptable. The test specimens should be compared with the required standards to determine if they meet the required specifications.
vii). Identification of blocks with efflorescence
If efflorescence is present on the test specimens, it indicates that the block may not have the desired quality and appearance. Blocks with efflorescence should be rejected and not used in construction.
viii). Repeat the test
In case of any doubts, the test should be repeated on a new sample of blocks to ensure that the results are accurate and consistent.
ix). Record keeping
The results of the efflorescence inspection should be recorded and maintained for future reference. This will help in tracking the quality of the blocks over time and identifying any trends or issues.
Efflorescence inspection is an essential part of quality control for AAC blocks. It is crucial to ensure that the blocks are free from efflorescence to ensure their quality and appearance. Any block with efflorescence should be rejected, while blocks without efflorescence can be used with confidence.
Accurate and consistent testing, record-keeping, and attention to detail are crucial for successful efflorescence inspection of AAC blocks.
8). Fire Resistant
Fire resistance is an important property of AAC blocks, making them ideal for use in constructions where fire safety is a concern. It is crucial to check the fire resistance of AAC blocks during quality control to ensure that the blocks meet the required specifications for their intended use.
AAC blocks are known for their excellent fire resistance properties, making them ideal for use in buildings with high fire risk. The fire resistance of AAC blocks can be tested by subjecting them to high temperatures and measuring their ability to resist fire. The blocks should have a fire-resistance rating of at least two hours.
In this section, we will discuss the detailed process of fire resistance inspection of AAC blocks.
i). Sampling
The first step in fire resistance inspection is sampling. Samples should be randomly selected from the batch of AAC blocks to ensure that the testing is representative of the entire batch.
ii). Testing Apparatus
The fire resistance of AAC blocks can be measured using a fire resistance test. The testing apparatus consists of a furnace, a temperature-measuring device, and a timer.
iii). Testing Procedure
The test specimens should be placed in the furnace, and the temperature should be raised to 750°C over a period of 30 minutes. The temperature should be maintained at 750°C for a period of 2 hours, and the timer should be used to record the time taken for the block to fail.
iv). Comparison with Standards
The fire resistance of AAC blocks should be at least 2 hours. The measured fire resistance of the block should be compared with the required standards to determine if it meets the required specifications.
v). Identification of blocks with low fire resistance
If the measured fire resistance of the block is lower than the required standard, it indicates that the block may not have the desired fire safety properties. Blocks with low fire resistance should be rejected and not used in constructions where fire safety is a concern.
vi). Repeat the test
In case of any doubts, the test should be repeated on a new sample of blocks to ensure that the results are accurate and consistent.
vii). Record Keeping
The results of the fire resistance inspection should be recorded and maintained for future reference. This will help in tracking the quality of the blocks over time and identifying any trends or issues.
Fire resistance inspection is an essential part of quality control for AAC blocks. It is crucial to ensure that the blocks meet the required fire resistance specifications to ensure their suitability for constructions where fire safety is a concern. Any block with low fire resistance should be rejected, while blocks with high fire resistance can be used with confidence.
Accurate and consistent testing, record-keeping, and attention to detail are crucial for successful fire resistance inspection of AAC blocks.
9). Dimensional Accuracy
Dimensional accuracy is an important property of AAC blocks, making them suitable for use in constructions where precise measurements are necessary. It is crucial to check the dimensional accuracy of AAC blocks during quality control to ensure that the blocks meet the required specifications for their intended use.
The dimensional accuracy of AAC blocks is critical for ensuring their proper fit and alignment during construction. The blocks should have a uniform size and shape, with straight edges and corners. The length, width, and height of the blocks should be within the specified tolerances.
In this section, we will discuss the detailed process of dimensional accuracy inspection of AAC blocks.
i). Sampling
The first step in dimensional accuracy inspection is sampling. Samples should be randomly selected from the batch of AAC blocks to ensure that the testing is representative of the entire batch.
ii). Preparation of test specimens
The samples should be cut to prepare test specimens with a size of 100mm x 100mm x 100mm using a diamond saw. The surface of the test specimens should be smooth and free from any defects or irregularities.
iii). Measuring the dimensions
The dimensions of the test specimens should be measured using a digital caliper with a precision of at least 0.1mm. The length, width, and height of each test specimen should be measured at three different points, and the average of these measurements should be recorded.
iv). Comparison with standards
The dimensions of AAC blocks should be within a tolerance of ± 1mm. The measured dimensions of the test specimens should be compared with the required standards to determine if they meet the required specifications.
v). Identification of blocks with low dimensional accuracy
If the measured dimensions of the test specimens are outside the required tolerance, it indicates that the block may not have the desired dimensional accuracy. Blocks with low dimensional accuracy should be rejected and not used in constructions where precise measurements are necessary.
vi). Repeat the test
In case of any doubts, the test should be repeated on a new sample of blocks to ensure that the results are accurate and consistent.
vii). Record keeping
The results of the dimensional accuracy inspection should be recorded and maintained for future reference. This will help in tracking the quality of the blocks over time and identifying any trends or issues.
Dimensional accuracy inspection is an essential part of quality control for AAC blocks. It is crucial to ensure that the blocks meet the required dimensional accuracy specifications to ensure their suitability for constructions where precise measurements are necessary. Any block with low dimensional accuracy should be rejected, while blocks with high dimensional accuracy can be used with confidence.
Accurate and consistent testing, record-keeping, and attention to detail are crucial for successful dimensional accuracy inspection of AAC blocks.
10). Durability
Durability is an important property of AAC blocks, making them suitable for use in constructions where longevity is a concern. It is crucial to check the durability of AAC blocks during quality control to ensure that the blocks meet the required specifications for their intended use.
In this section, we will discuss the detailed process of durability inspection of AAC blocks.
i). Sampling
The first step in durability inspection is sampling. Samples should be randomly selected from the batch of AAC blocks to ensure that the testing is representative of the entire batch.
ii). Accelerated weathering test
The durability of AAC blocks can be measured using an accelerated weathering test. The testing apparatus consists of a UV chamber, a spray nozzle, and a temperature-measuring device.
iii). Testing procedure
The test specimens should be placed in the UV chamber, and the temperature should be raised to 50°C. The specimens should be exposed to UV light for a period of 1000 hours. At the end of the exposure period, the specimens should be sprayed with water for a period of 2 hours, and the temperature measuring device should be used to measure the temperature of the specimens.
iv). Comparison with standards
The durability of AAC blocks should be such that they can withstand exposure to UV light and water for a prolonged period without any significant deterioration. The measured durability of the block should be compared with the required standards to determine if it meets the required specifications.
v). Identification of blocks with low durability
If the measured durability of the block is lower than the required standard, it indicates that the block may not have the desired longevity properties. Blocks with low durability should be rejected and not used in constructions where longevity is a concern.
vi). Repeat the test
In case of any doubts, the test should be repeated on a new sample of blocks to ensure that the results are accurate and consistent.
vii). Record keeping
The results of the durability inspection should be recorded and maintained for future reference. This will help in tracking the quality of the blocks over time and identifying any trends or issues.
Durability inspection is an essential part of quality control for AAC blocks. It is crucial to ensure that the blocks meet the required durability specifications to ensure their suitability for constructions where longevity is a concern. Any block with low durability should be rejected, while blocks with high durability can be used with confidence.
Accurate and consistent testing, record-keeping, and attention to detail are crucial for the successful durability inspection of AAC blocks.
Thank you for taking the time to read this educational blog post about the AAC Blocks Quality Checklist. We hope that you found it informative and engaging. If you have any questions or comments, please feel free to leave comments in the comment section below. Don’t forget to check out our other educational posts on myengineeringsupport.com for more learning opportunities!
Bar Bending Schedule (BBS) Basics Part -1
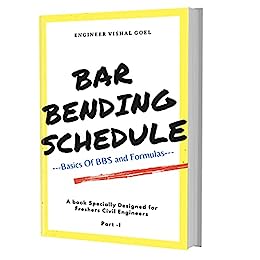
I hope this information can be useful for you guys.
If you like this article then please share it with your friends & also like our Facebook Page and join our Telegram Channel.
If you want a PDF copy of this, Do let’s know by commenting & you can message us on our Instagram & telegram channel, or you can download it from the top right-hand corner of this post.
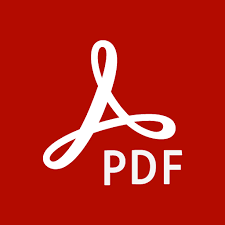
Thanks For the Great Attention!
Good Bye & Take Care
Happy Learning
Also, Read,
AAC Blocks Manufacturing Process – An Ultimate Guide
28 Important Comparison between WPC and PVC Wall Panel
MDF VS Particle Board – 15 Important Differences
Flush Door vs Wooden Panel Door
UPVC vs Aluminium vs Wooden Windows
Related Video
You really make it seem so easy with your presentation but I find this topic to be really something that I think I would never understand. It seems too complex and extremely broad for me. I’m looking forward for your next post, I’ll try to get the hang of it!